DEYING MOLD not only provide Ballistic Helmet mould fabrication,but also provide PROCESS OF THE MAKING BULLETPROOF HELMETS.To make a bulletproof helmet;
First of all, you need a bulletproof helmet mold and a hydraulic press;
Second,getting the required number of fibre sheets. Using resin, the fibre sheets are impregnated for properly binding the layers together. These fibre sheets are further cut into different shapes and sizes. The shapes can then be used in a mold and pressed for creating the helmet shape.
We have explained the process in brief above using a simplified approach; however, the actual process is significantly more complex. Nevertheless, a broad overview of the manufacturing process of ballistic helmets or bulletproof helmets has been provided.
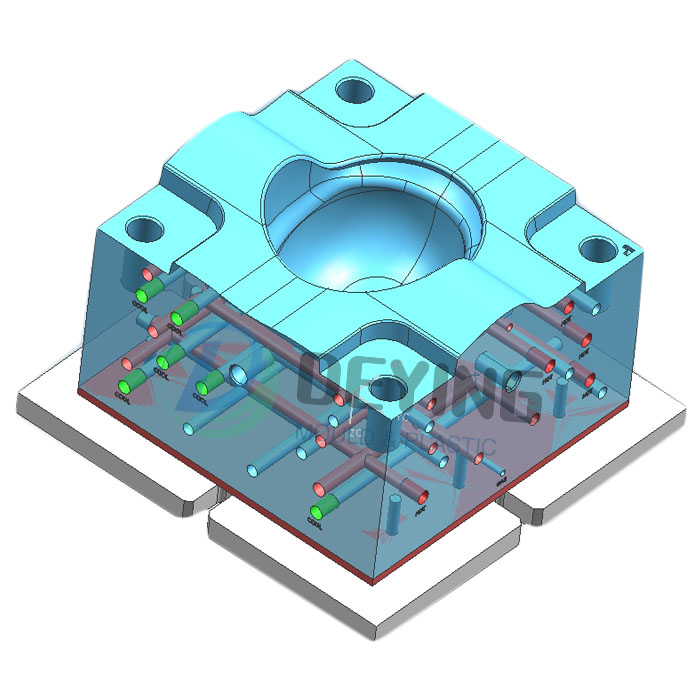
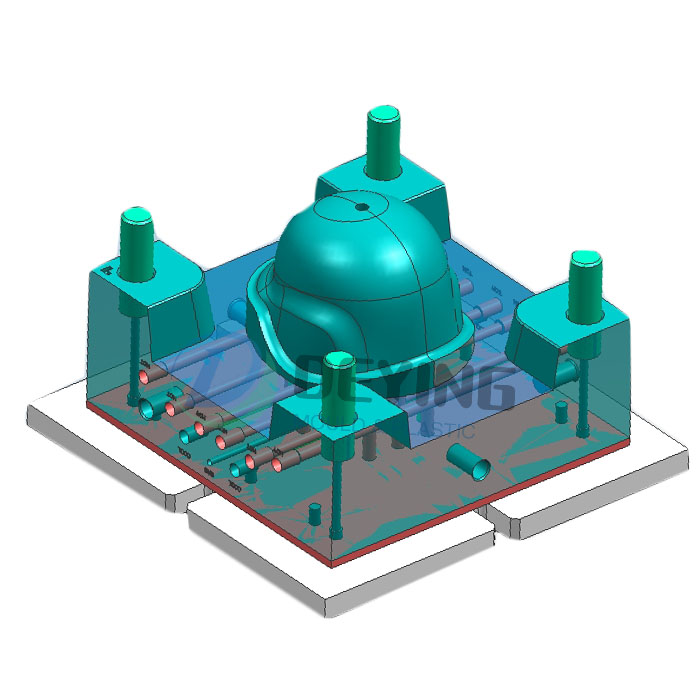
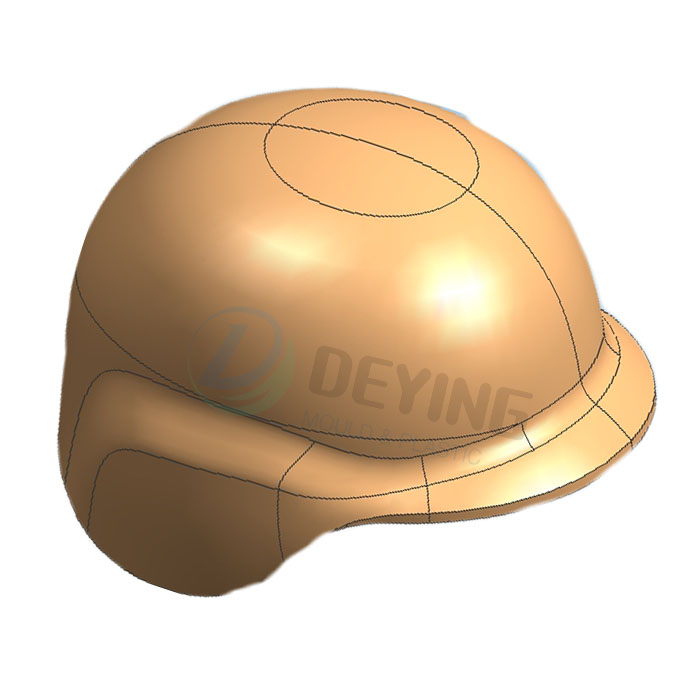
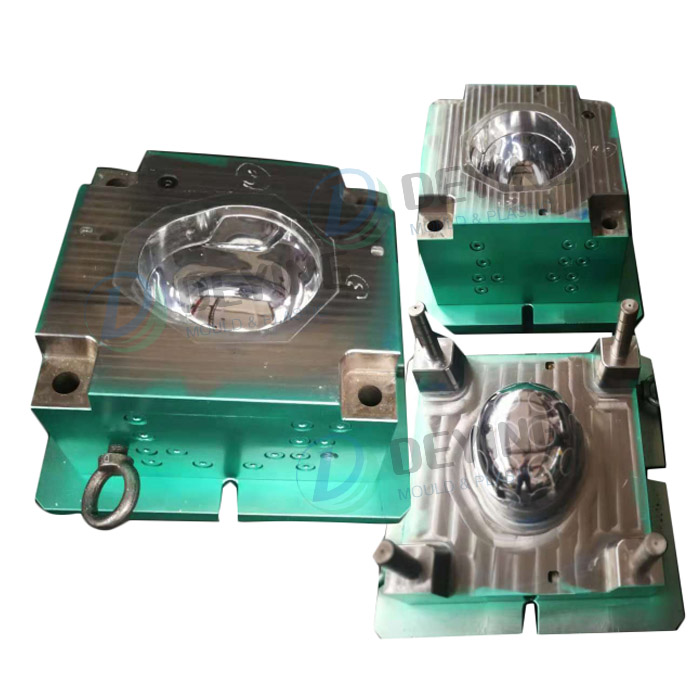
Compression molding is a method of molding in which the molding material, generally preheated, is first placed in an open, heated mold cavity. The mold is closed with a top force or plug member, pressure is applied to force the material into contact with all mold areas, while heat and pressure are maintained until the molding material has cured.
UD/KEVLAR product mould
UHMWPE is commonly known as very high molecular weight polyethylene. Its molecular weight can reach 1 to 5 million. It has high wear resistance, low friction coefficient, high impact resistance, and better sound-absorbing performance. Compared with ordinary thermoplastics, it has lower fluidity and is difficult to process. At present, it can only be produced by molding. Our company cooperated with the *** unit, using its good impact resistance, developed the body armor and bulletproof helmet molds, realized segmented pressurization and heating on a pair of molds, and switched the heating mold to cooling in the later stage of molding. The mold ensures that the product is cooled and shaped to the set temperature and set material hardness, ensuring that the product can be easily taken out of the mold.
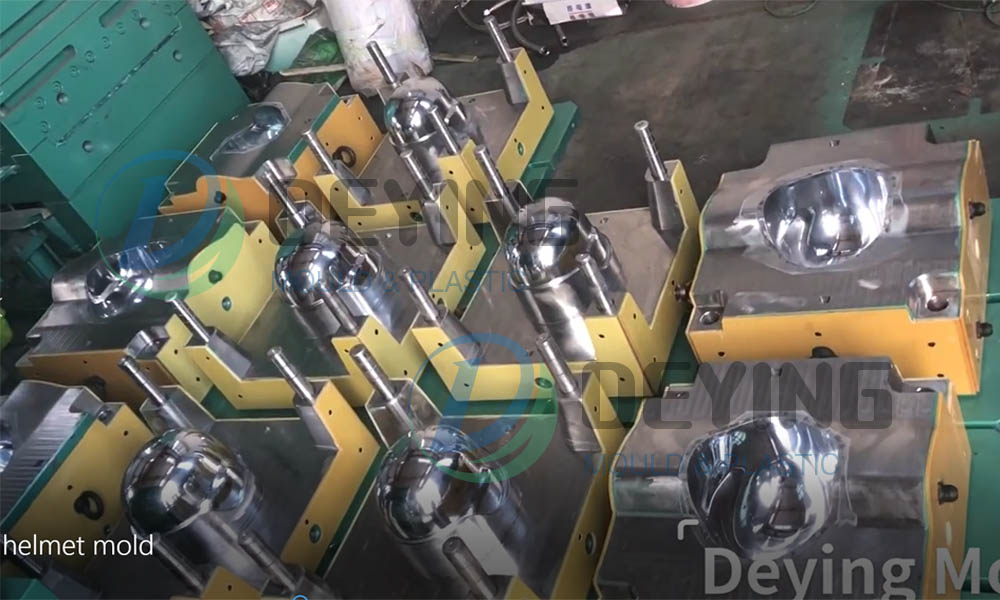
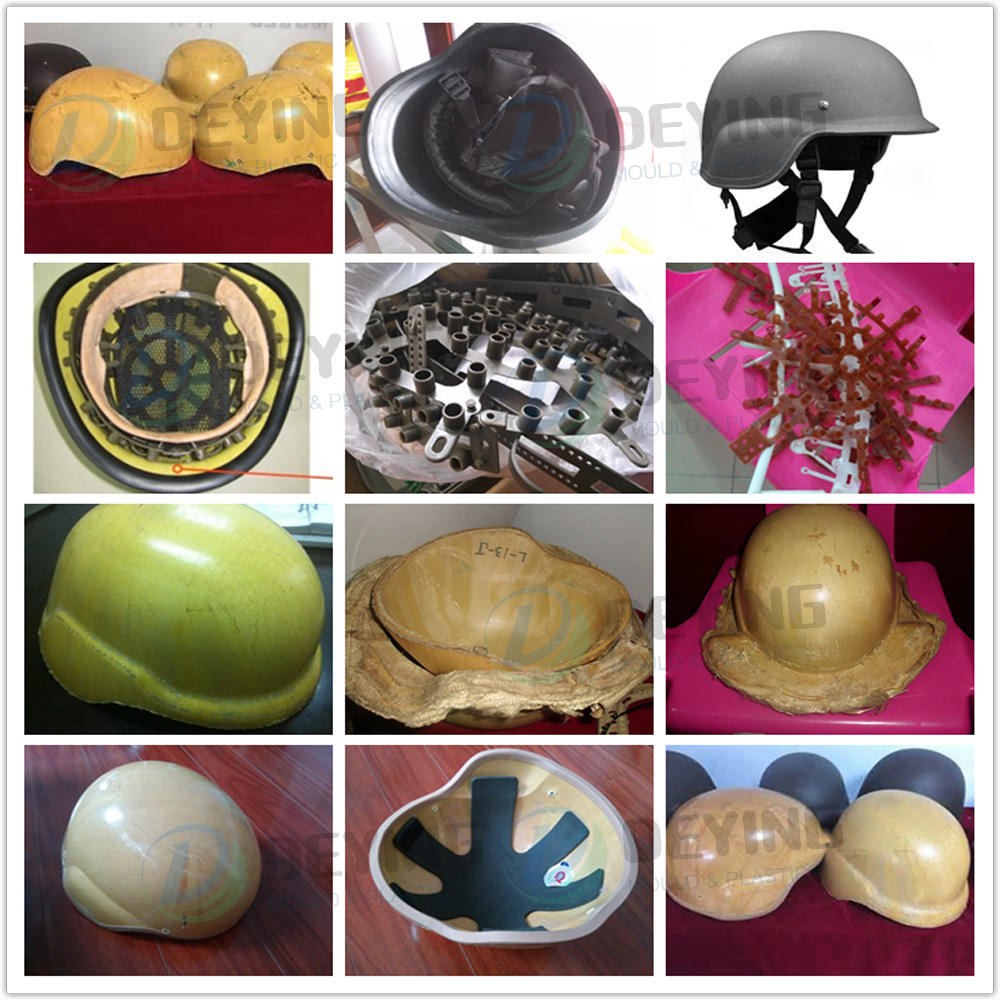
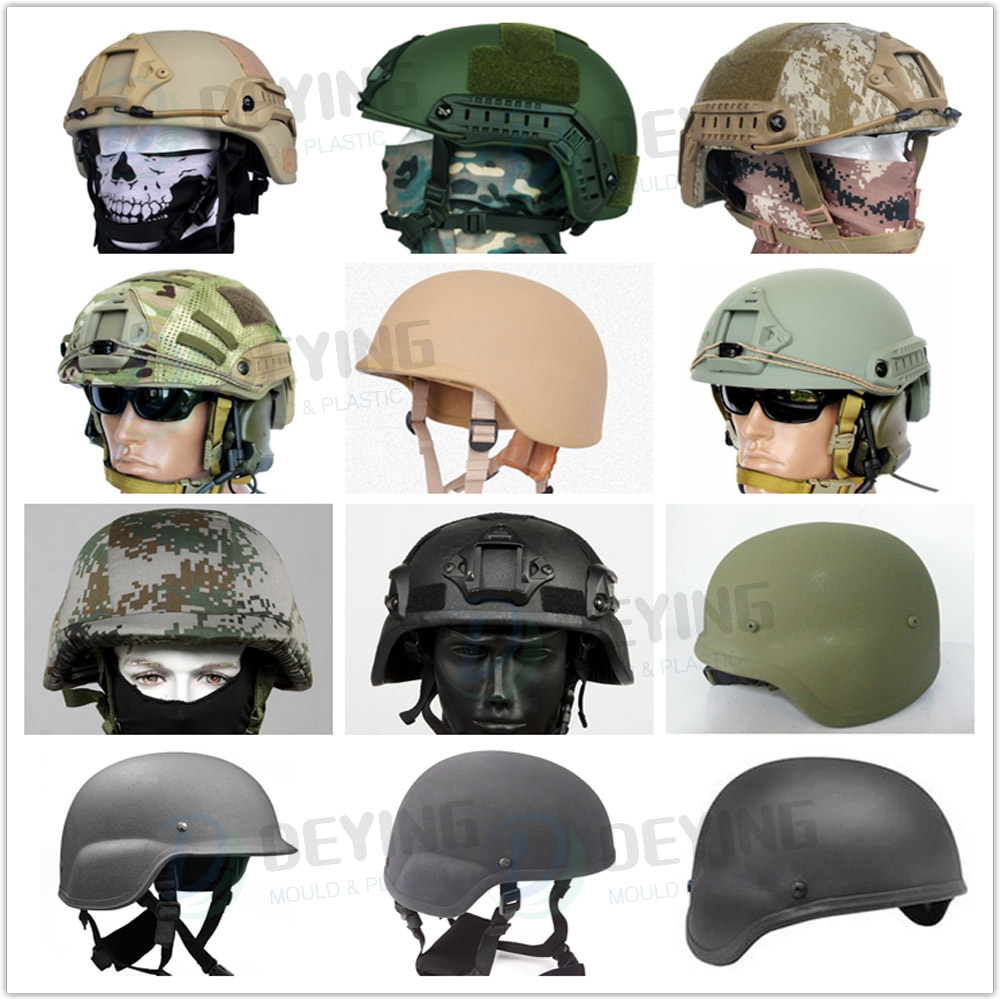
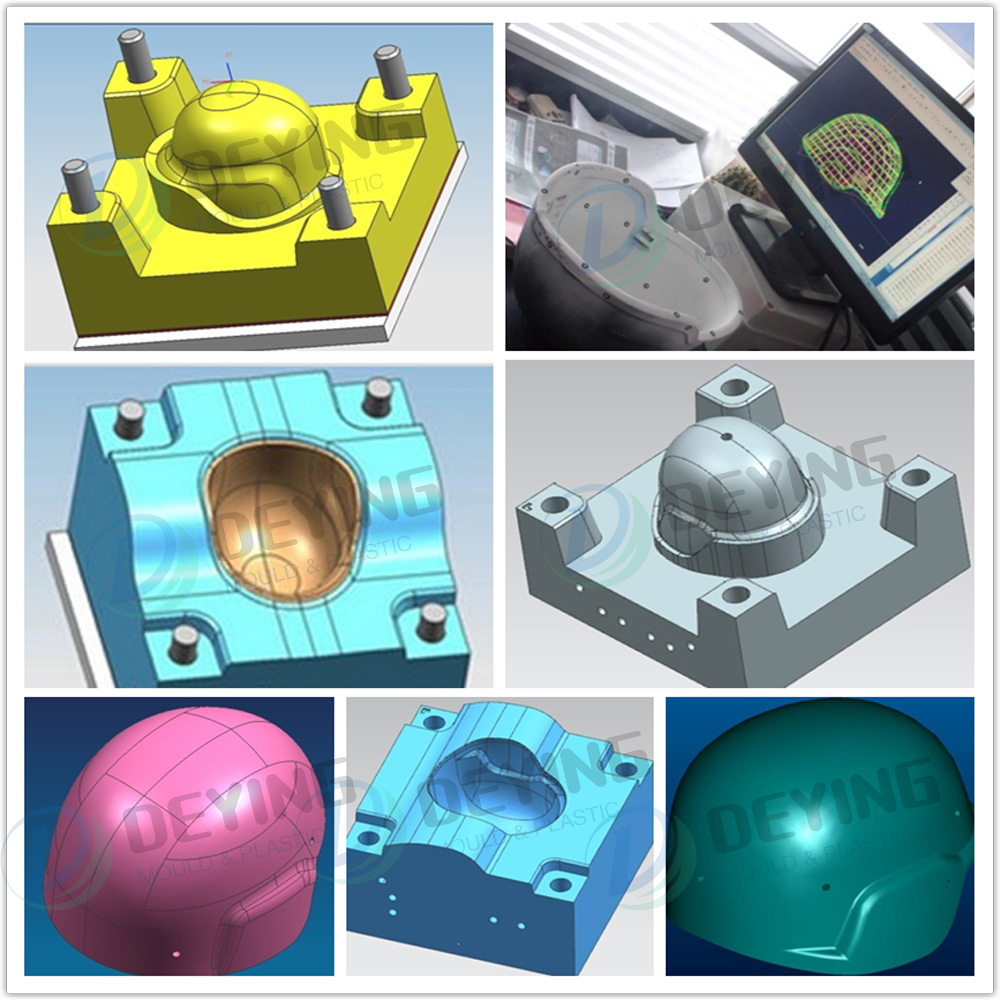
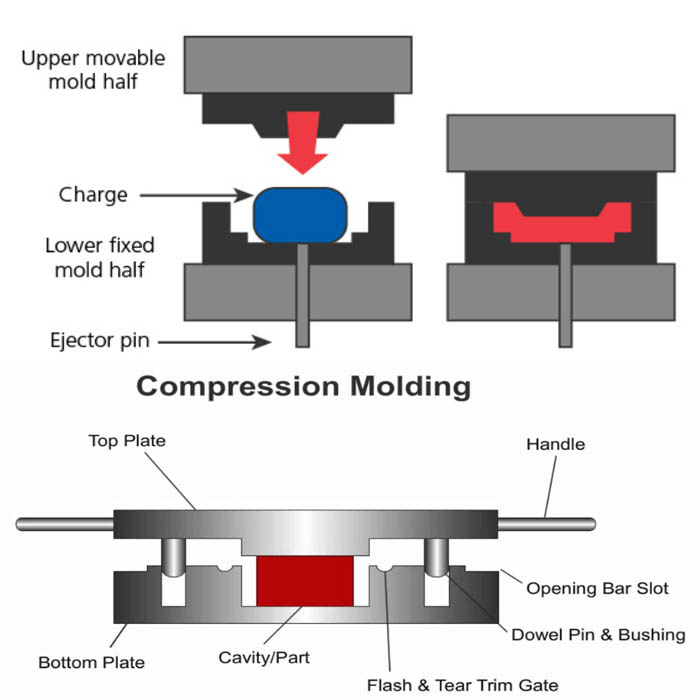
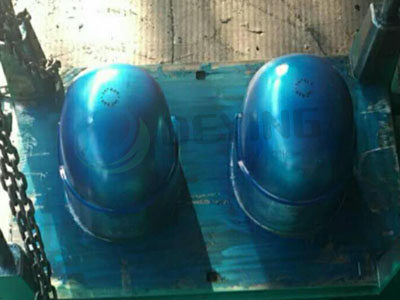
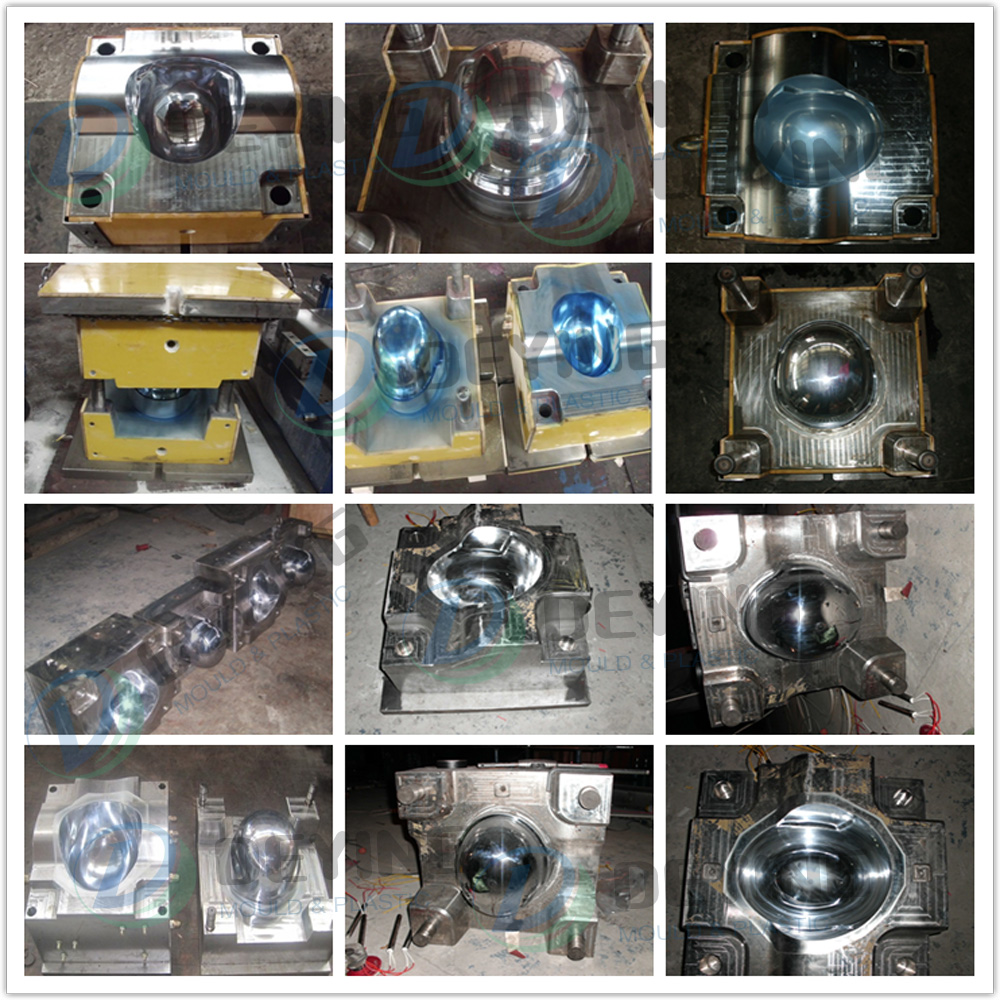
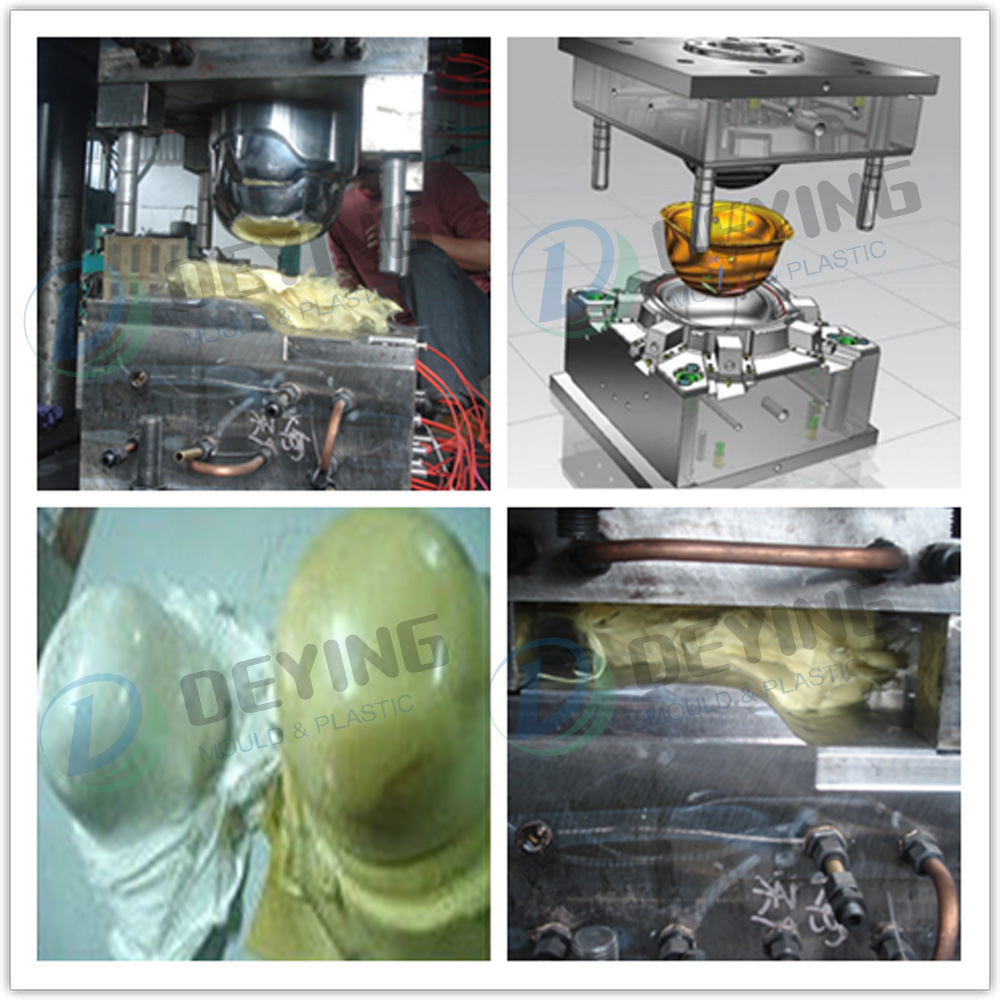
MB/Wechat/Whatsapp:+0086-13456489912
sophiemould@foxmail.com
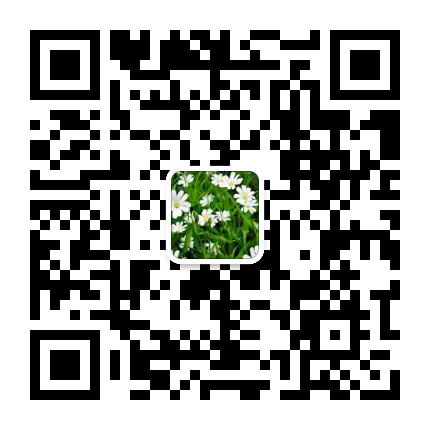
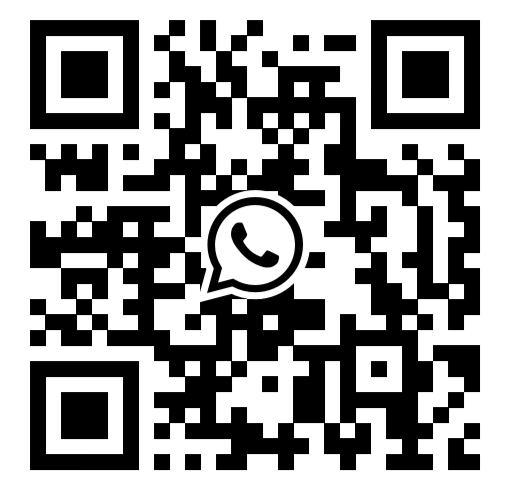