Melt blown cloth, commonly known as the "heart" of masks, and melt blown die head is the core hardware of the melt blown cloth production line. In order to meet market demand, Rongyi has launched a new meltblown die head suitable for standard fabric widths from 650 to 1800 mm
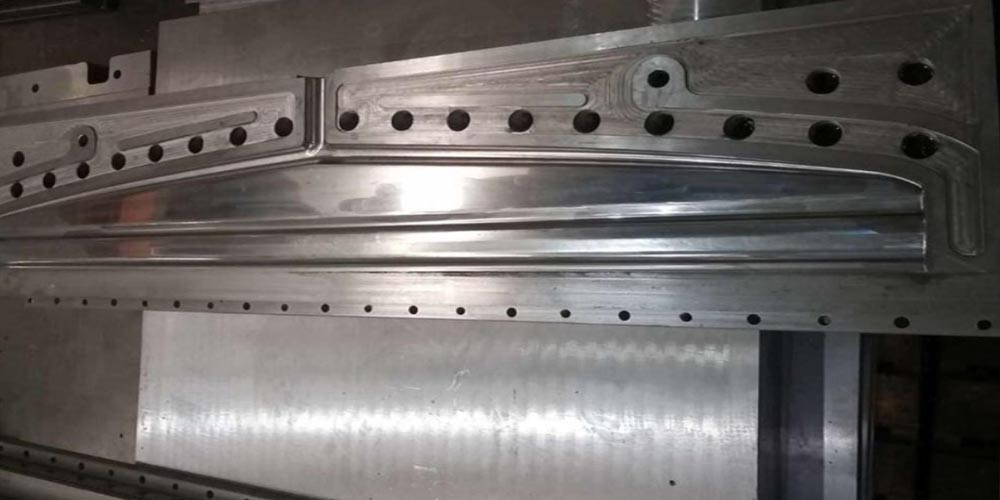
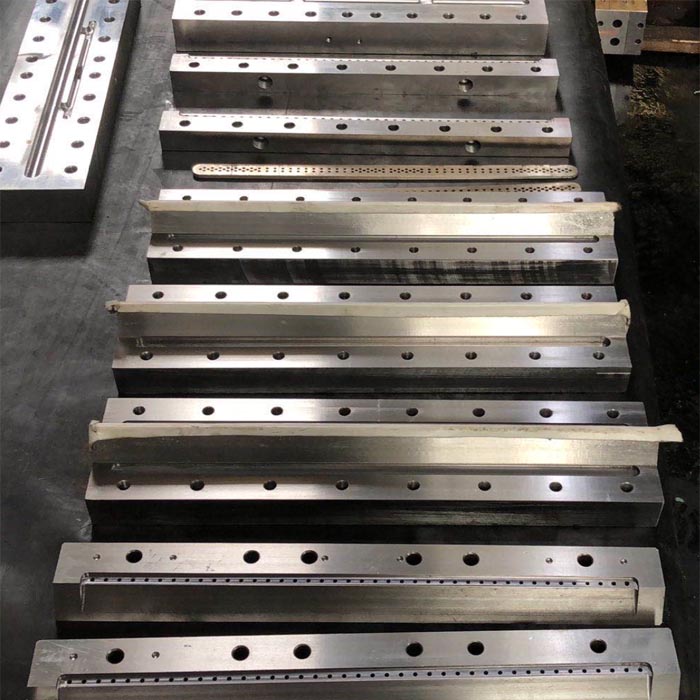
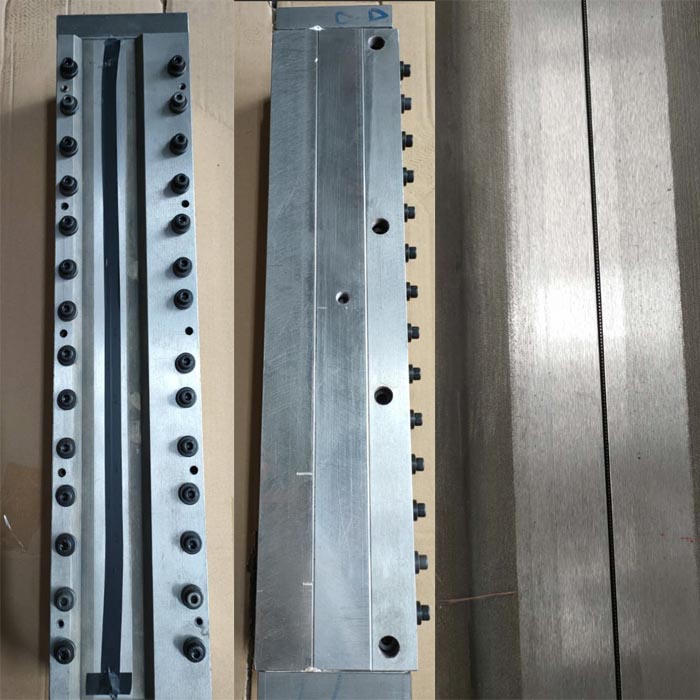
How to judge the quality of extrusion die mold ?
The use of extrusion molds is also very common. If you do not notice the quality of the selection when using it, it will seriously affect the normal use of the extrusion mold. In order to make the mold use well, the following provides relevant judgments about extrusion The specific way of mold quality is good or bad.
First, look at the thickness of the mold. Although the mold does not need to be used too vigorously or other harsh environments, because of the repeated mold release, the mold is very easy to wear, deform, and destroy. The fundamental way to solve this problem is to thicken the thickness of the mold, so the grade of the mold can be clearly distinguished by looking at the thickness.
Second, see if the specifications of the extrusion mold are standard. A good mold can control the size of the extruded plastic product produced within a few tenths of a millimeter error, while the inferior mold often produces a product error of a few millimeters or even a few millimeters. A few centimeters.
Third, check the material and workmanship of the entire mold. A good mold should be very smooth on both sides, look shiny, and feel slightly moist and sinking. Inferior molds may have burrs or pits on the surface. Compare the two. It's just standing on top of each other.
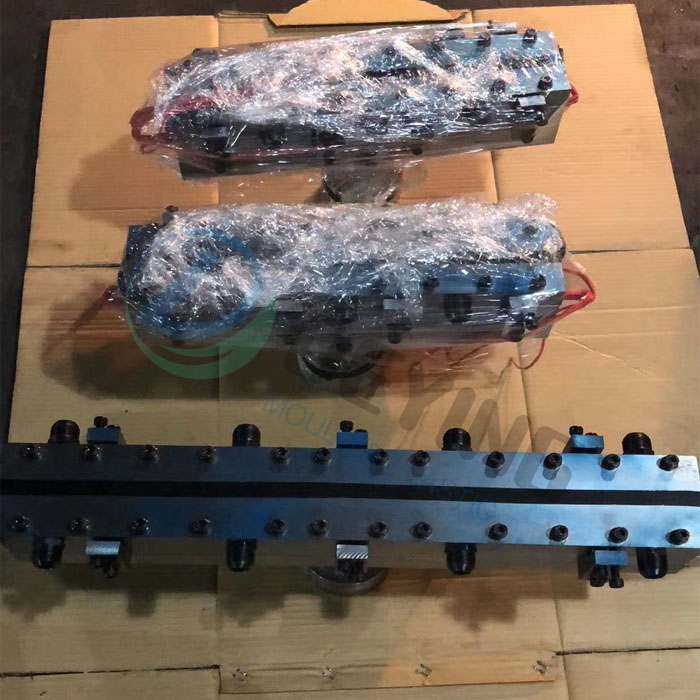
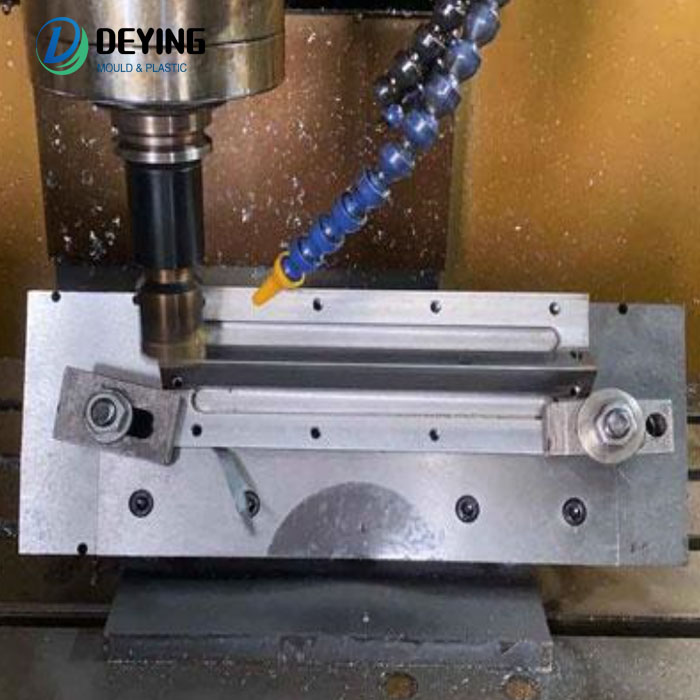
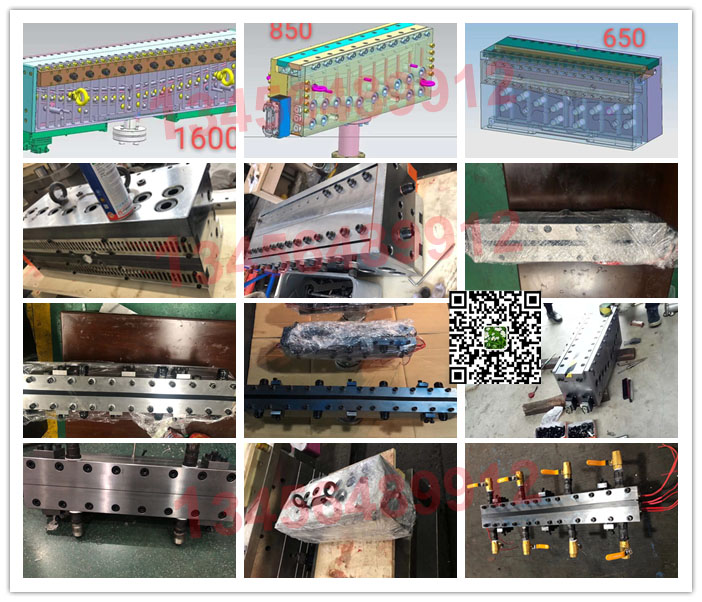
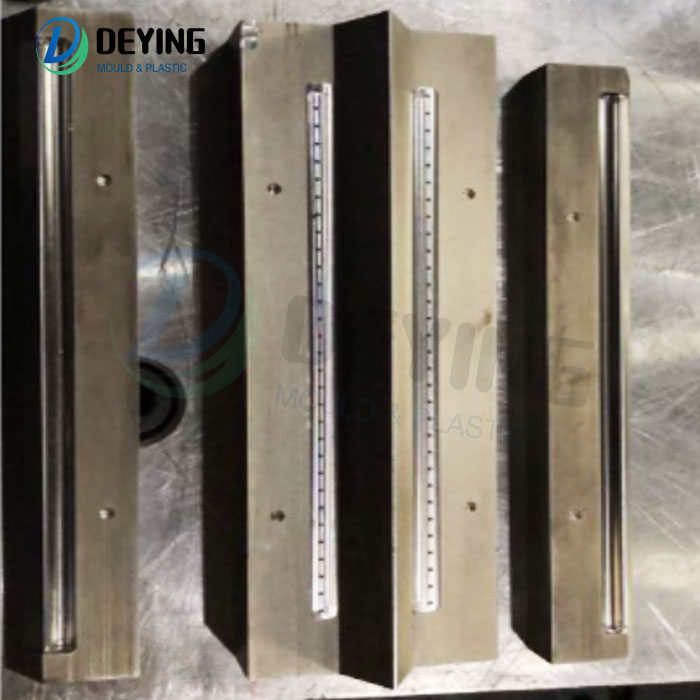
Melt blown spinneret size:
Length 300mm and 450mm,650mm,850mm are available
Feeding hole: drilled with 0.2mm diameter electrode tube , finished diameter during 0.25-0.26mm.
Melt-blown nonwoven fabric is made by entangling fibers while extruded material from the spinneret in the same time blowing hot air. The common application is face masks, industrial filters, etc.
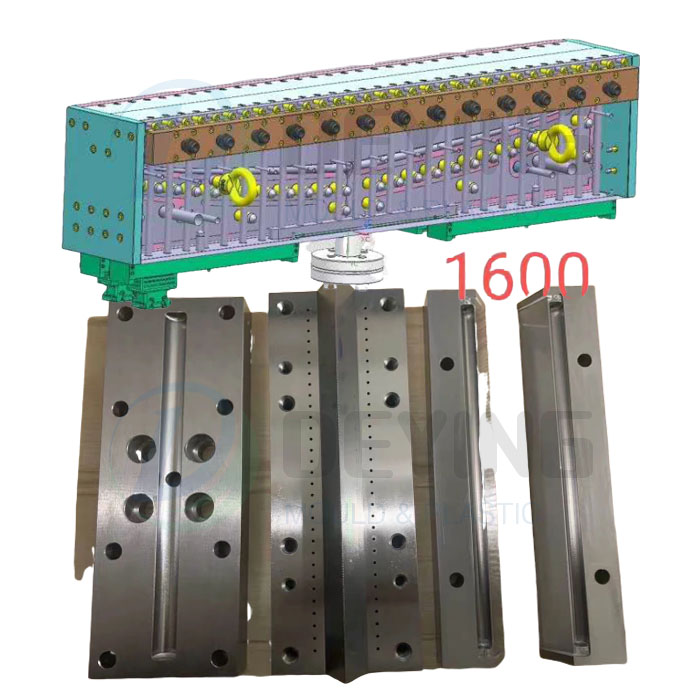
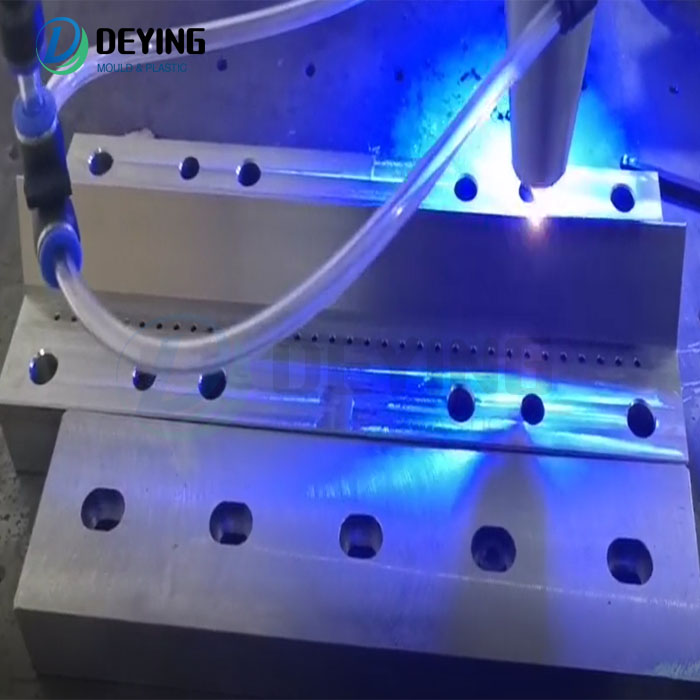
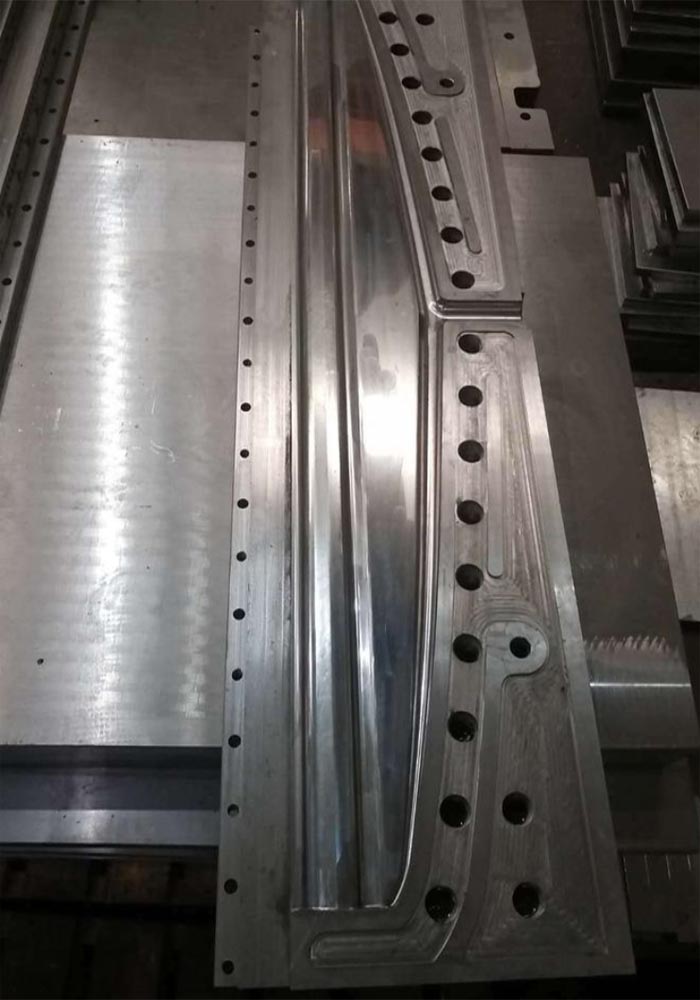
Infect by CORNA-19 epidemic, masks are very limited, no matter the FFP3, FFP2, N95, KN95 KN90, surgical mask; medical mask, ordinary masks/respirator, all masks are lack.
Mask making machines are working every day every 24 hours, the consumables and spare parts in stock are very necessary to keep the machine running.
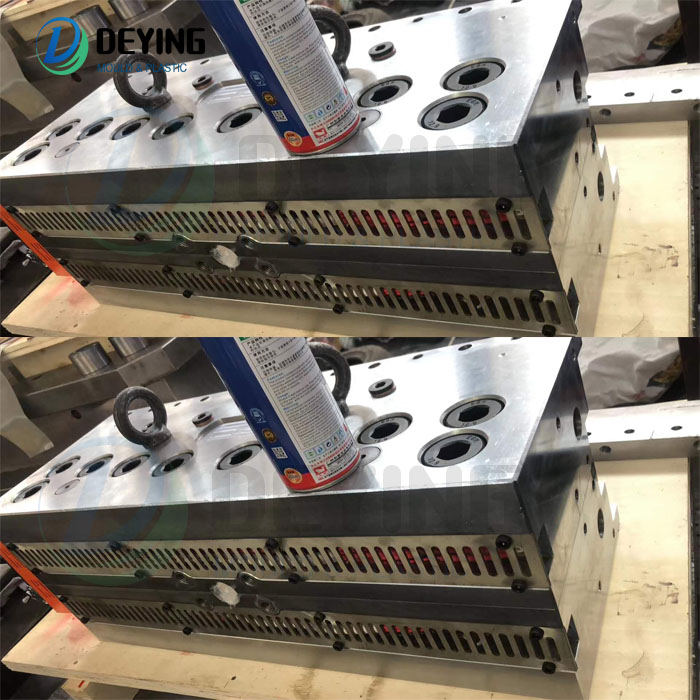
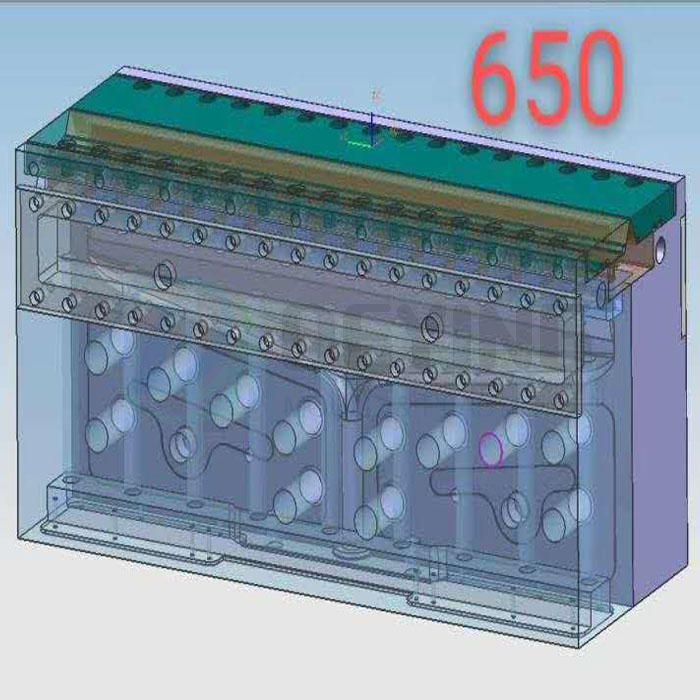
The equipment of the continuous production line of meltblown nonwovens is about 6m high, 5m wide, and 20m long. The production equipment is as follows:
(1) Screw extruder: The screw diameter is generally 100-120mm, and the length/diameter ratio is 30. Its purpose is to melt the slices.
(2)Metering pump: Its function is to accurately measure, control the output and the fineness of the fiber. It is a gear pump that continuously delivers the melt to the spinneret. (3)Melt filter: Its function is to filter out impurities in the melt to avoid clogging the spinneret holes.
(4)Conveying net curtain: The melt blown fiber is evenly received and spread on the net, and transported forward. There is a suction fan under it to discharge the hot air coming down from the top.
(5)Spinning box: It is the key equipment of the melt-blown process. There is a strip-shaped spinneret, which is covered with a long row of spinneret holes. Generally, there are about 1500 nozzle holes per m. The two sides of the spinneret are equipped with hot air nozzles, and there are hot air nozzles underneath, which form an angle of 50b with the nozzle holes. After the fiber is ejected, the high-speed hot air is used to stretch the air flow immediately to blow the fiber and become superfine fiber.
(6)Feeding system: It is composed of 3 measuring hoppers, which are used to measure white slices, masterbatch, and additives. The 3 components enter the mixing mixer below to mix evenly, and then put into production.
(7)Hot air blower and heater: provide the temperature and pressure of the hot air used in the spinning airflow drawing, use electricity to heat, and consume a lot of power.
(8)The coiling machine adopts automatic coiling, and the melt blown cloth is packaged in rolls. Meltblown nonwovens are characterized by ultra-fine fibers, and the smallest fiber diameter can reach 0.5Lm, generally between l-5Lm. The finer the fiber, the better the quality of meltblown cloth, but the output is relatively reduced. Because the fiber is ultrafine, its specific surface area is large, and the adsorption capacity is strong, which is the most prominent advantage of melt blown cloth.
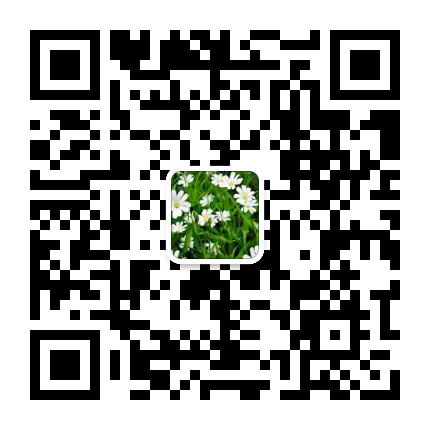
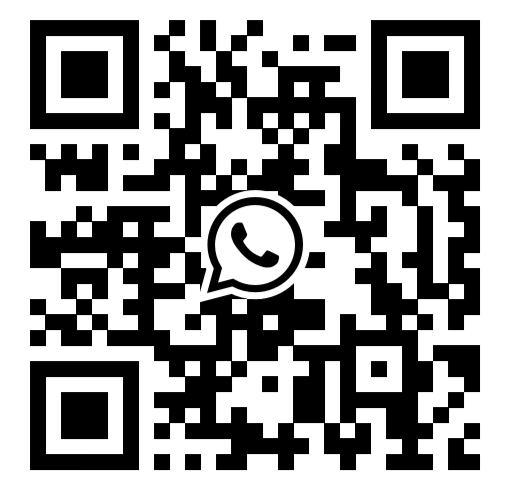
MB/Wechat/Whatsapp:+0086-13456489912
sophiemould@foxmail.com