The production of Mich Ach Aramid Military helmet mold is to put Kevlar or UHMWPE material on the filler that feeds the device. These thermosetting materials need to use a check valve, and then the composite material is injected into the semi-closed mold to fill the cavity. And aggregate. After thorough curing, the hot product is demolded and made.
We will provide you with: timely reply to letters, phone calls or faxes, provide quotations and mold design plans, conduct technical exchanges, send mold processing pictures and plans, test molds and send samples, and deliver them in time.
Provide customers with data, pictures, movies, and mold progress on a regular basis every week.
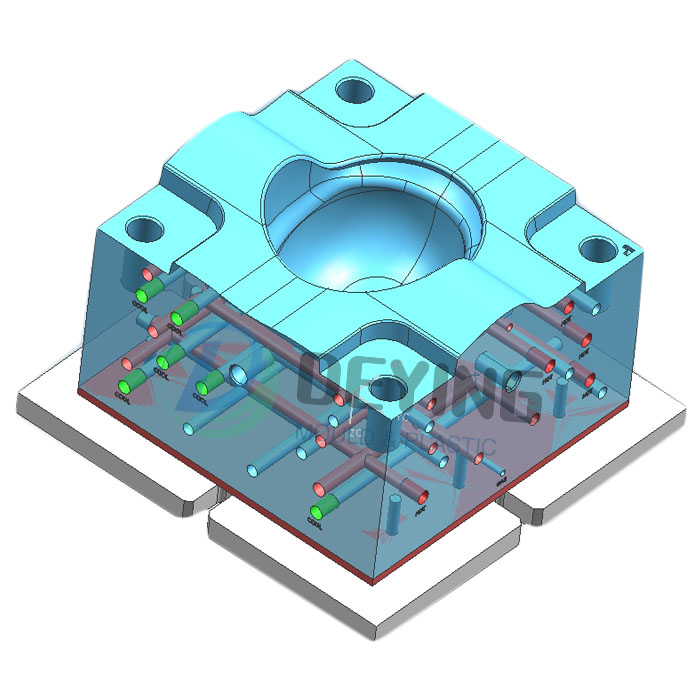
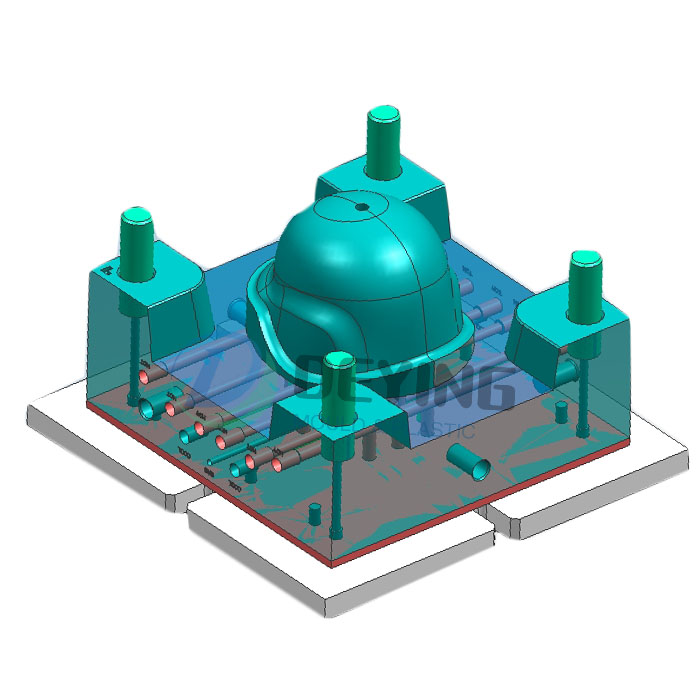
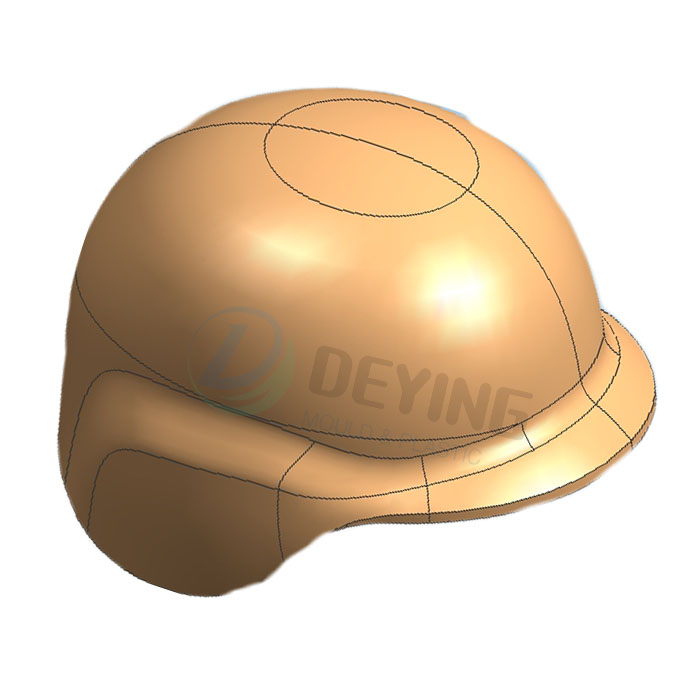
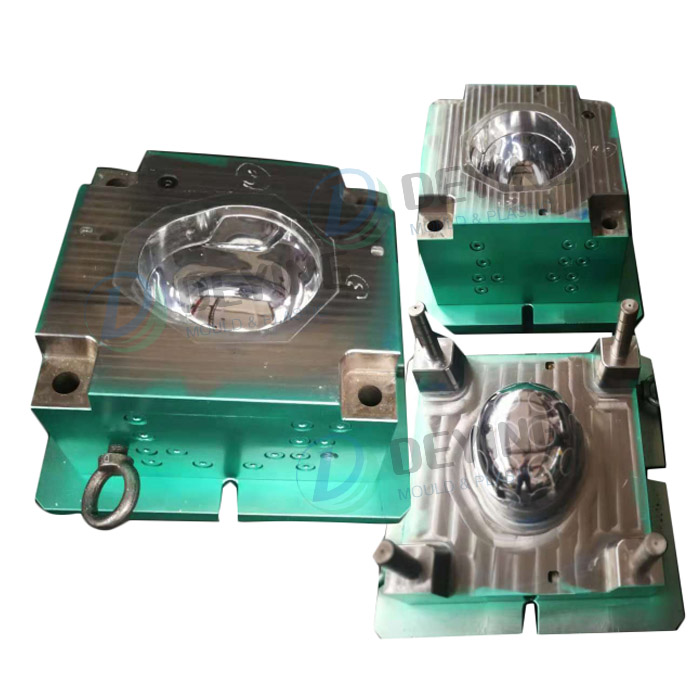
Compression molding is a method of molding in which the molding material, generally preheated, is first placed in an open, heated mold cavity. The mold is closed with a top force or plug member, pressure is applied to force the material into contact with all mold areas, while heat and pressure are maintained until the molding material has cured.
UD/KEVLAR product mould
UHMWPE is commonly known as very high molecular weight polyethylene. Its molecular weight can reach 1 to 5 million. It has high wear resistance, low friction coefficient, high impact resistance, and better sound-absorbing performance. Compared with ordinary thermoplastics, it has lower fluidity and is difficult to process. At present, it can only be produced by molding. Our company cooperated with the *** unit, using its good impact resistance, developed the body armor and bulletproof helmet molds, realized segmented pressurization and heating on a pair of molds, and switched the heating mold to cooling in the later stage of molding. The mold ensures that the product is cooled and shaped to the set temperature and set material hardness, ensuring that the product can be easily taken out of the mold.
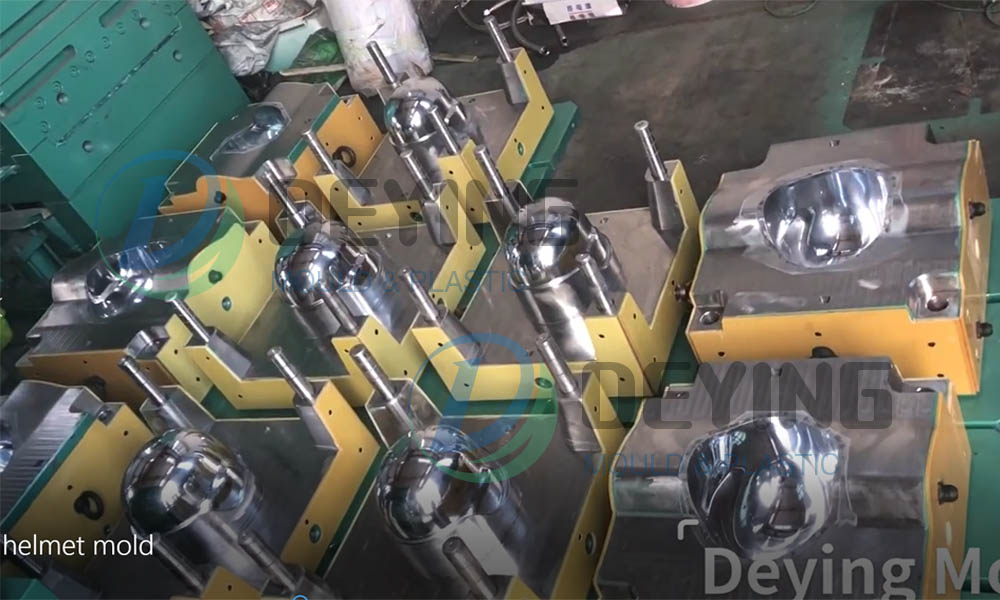
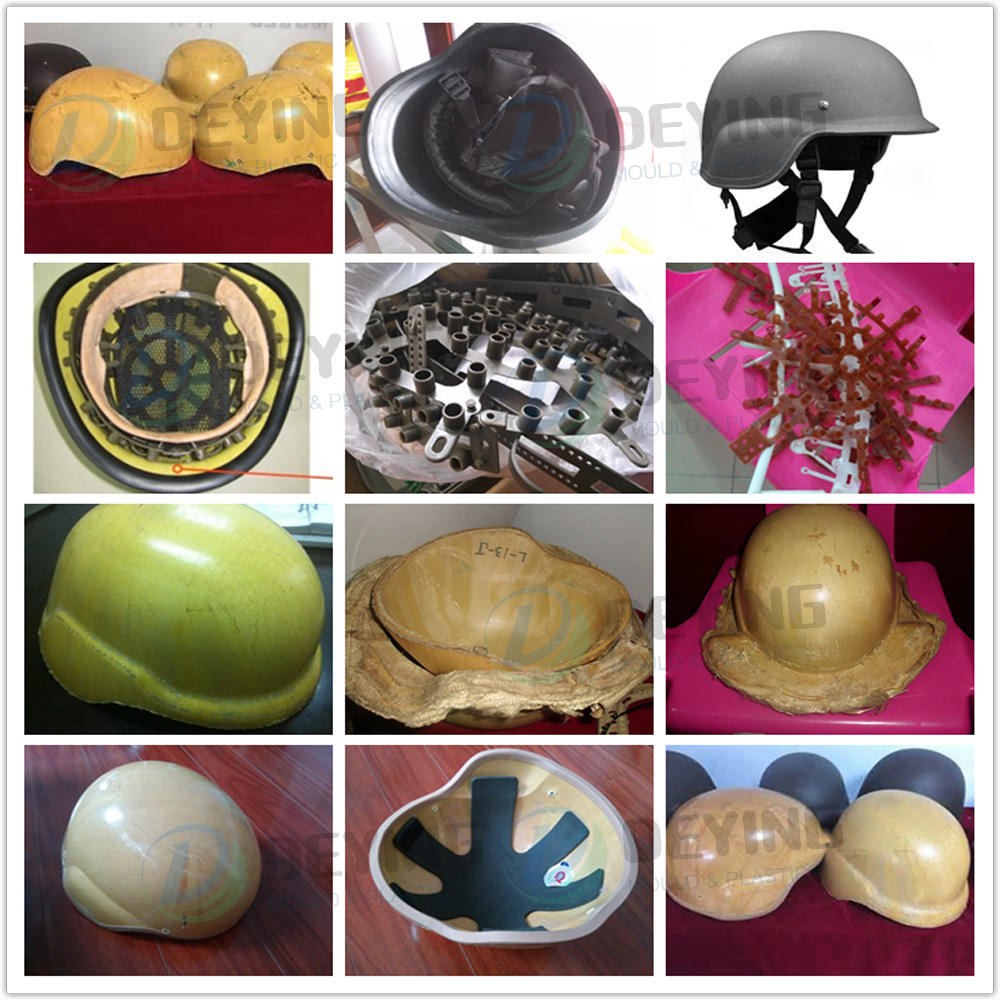
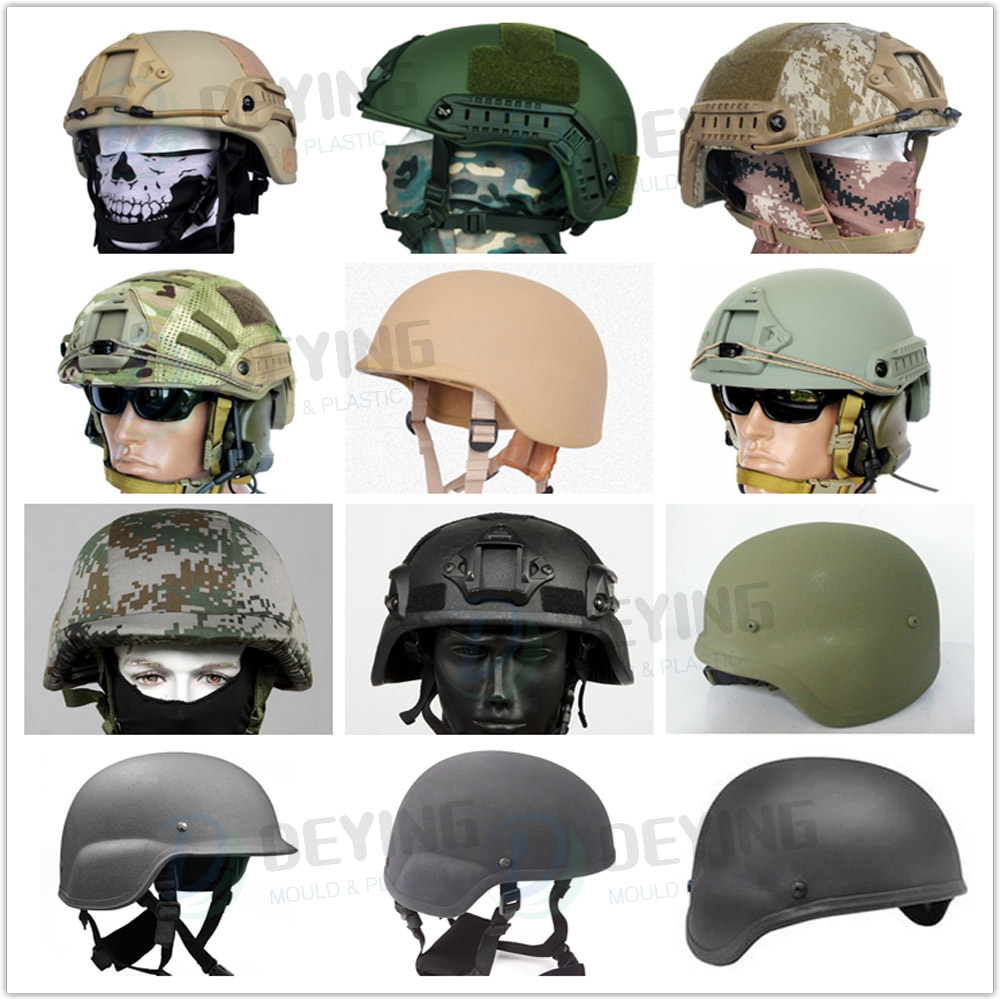
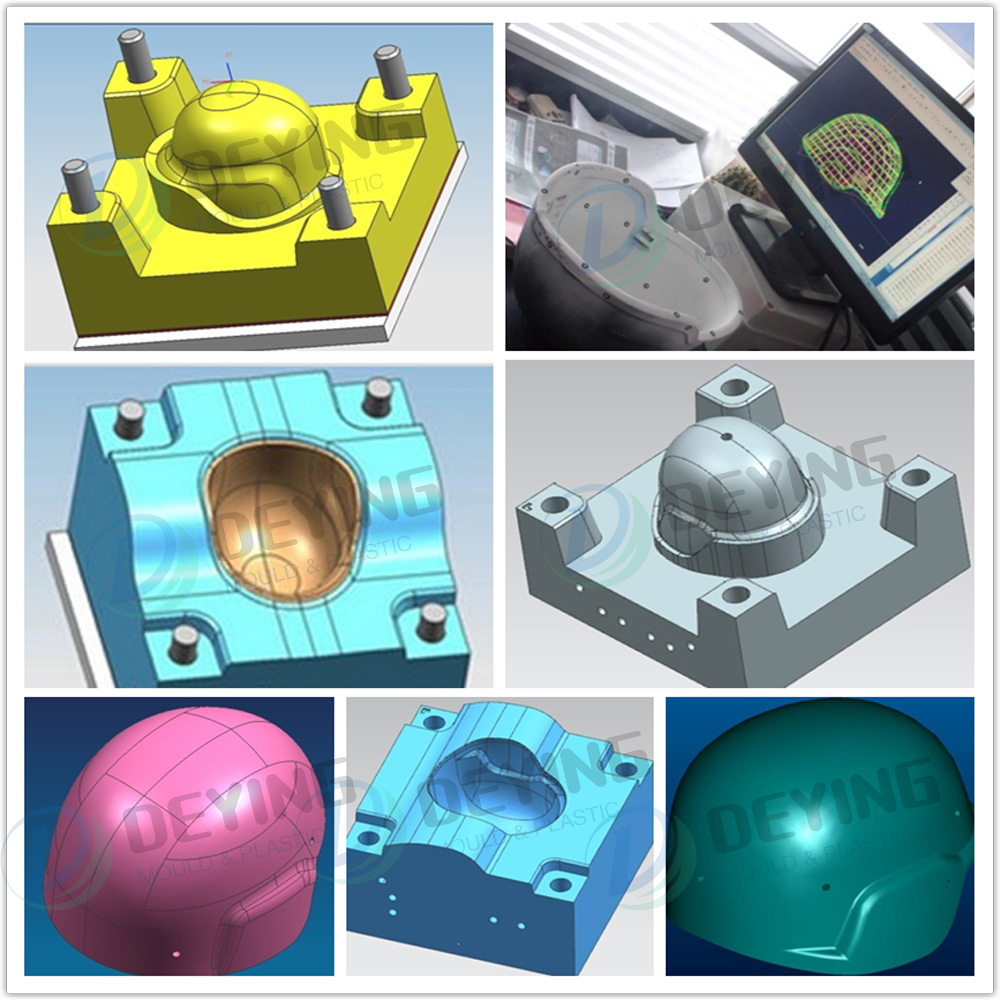
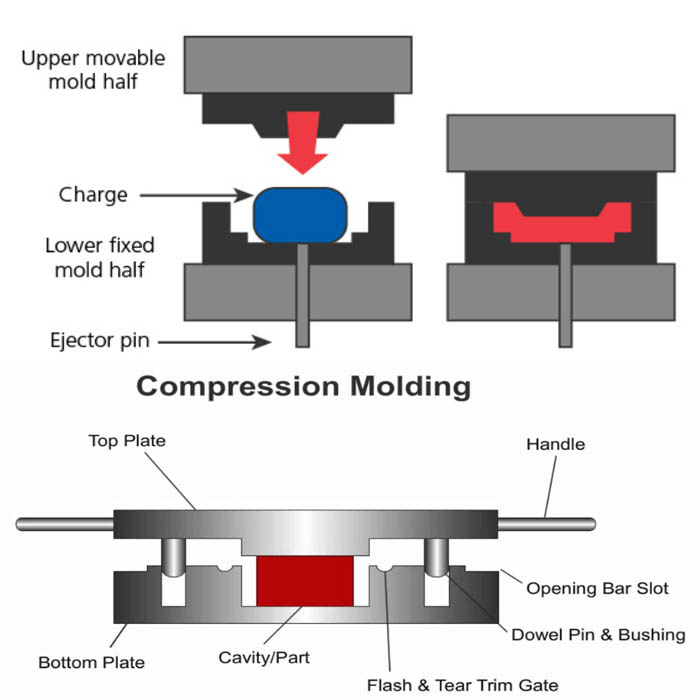
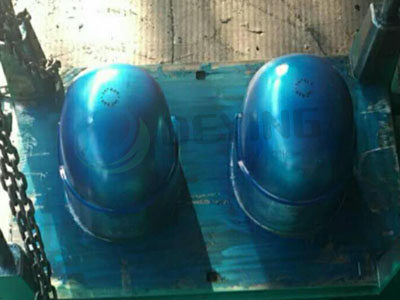
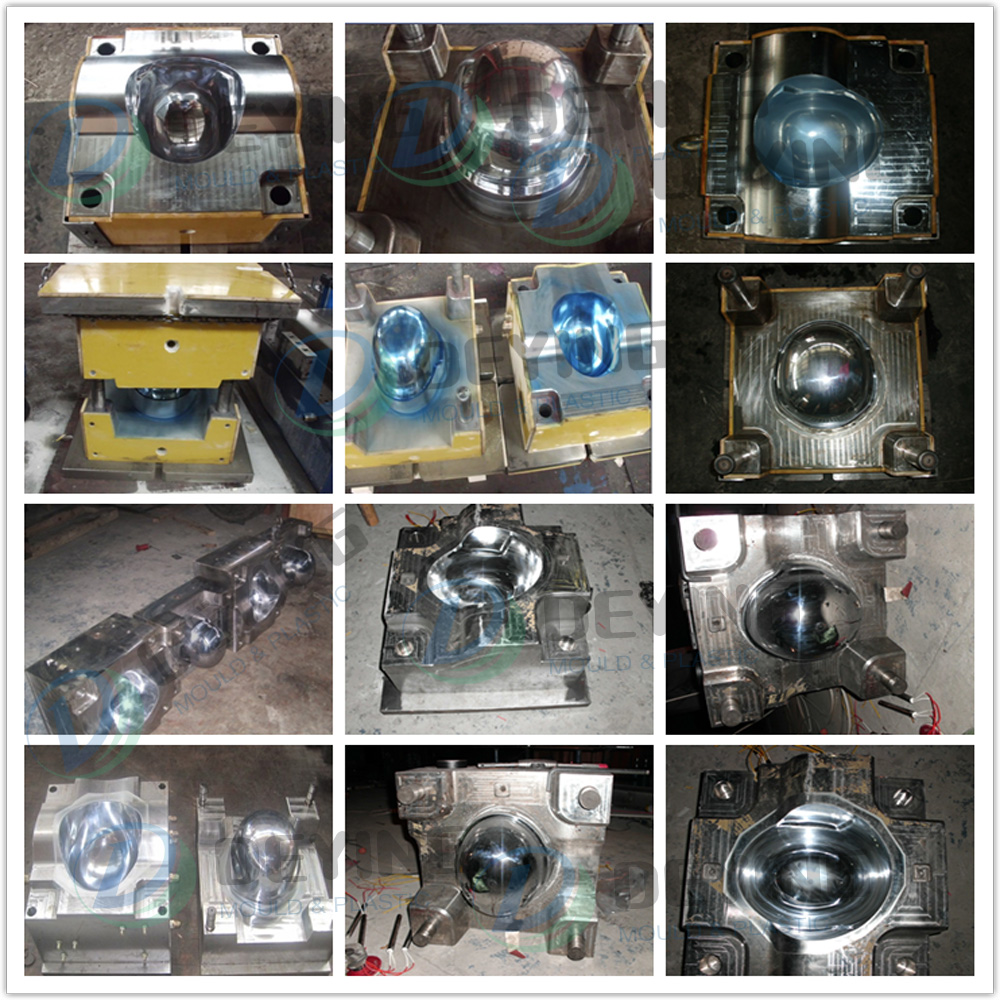
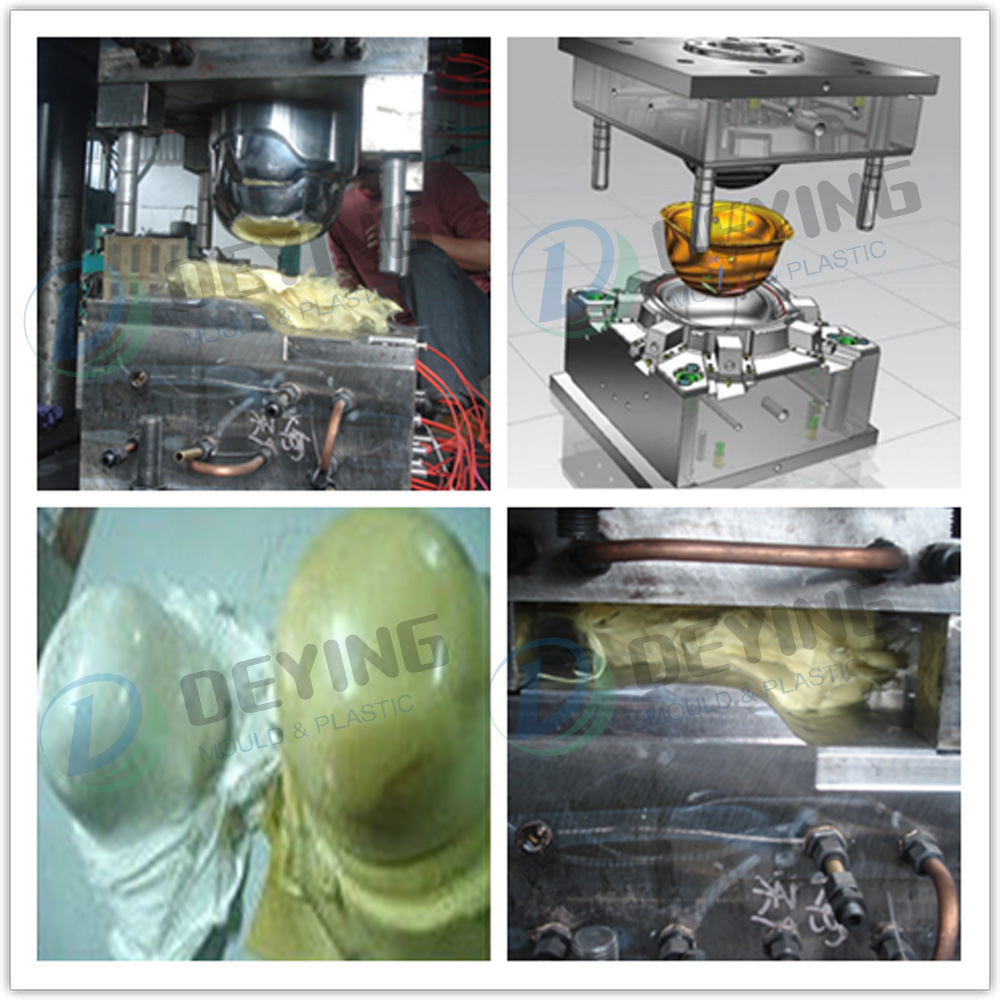
MB/Wechat/Whatsapp:+0086-13456489912
sophiemould@foxmail.com
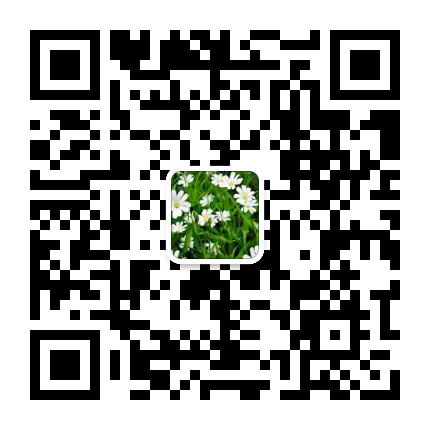
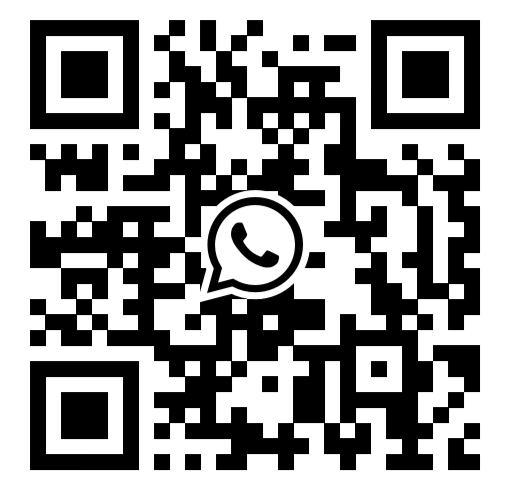