Compression molding Process- Advantages and Disadvantages
Compression molding is a well known technique to develop variety of composite products. It is a closed molding process with high pressure application. Heat and pressure is applied as per the requirement of composite for a definite period of time. The material placed in between the molding plates flows due to application of pressure and heat and acquires the shape of the mold cavity with high dimensional accuracy which depends upon mold design. Curing of the composite may carried out either at room temperature or at some elevated temperature. After curing, mold is opened and composite product is removed for further processing.
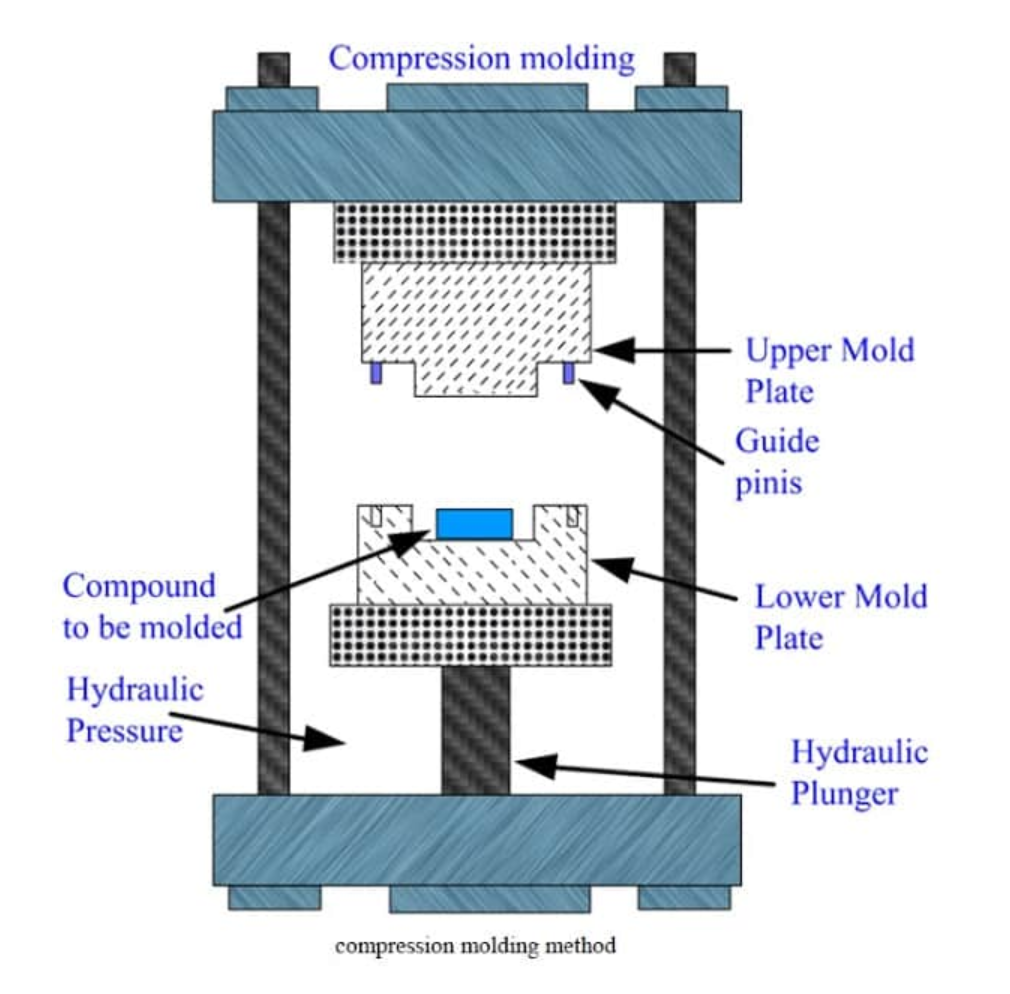
In principle, a compression molding machine is a kind of press which is oriented vertically with two molding halves (top and bottom halves). Generally, hydraulic mechanism is used for pressure application in compression molding.
What is a compression?
DEYING is a high-quality mold manufacturer, and provides solutions for various molds, such as thermoplastic molds, thermoset molds, glass reinforcement molds, carbon fiber molds, etc.
So what is a compression? Compression mold is a type of mold that forms a solidified material by compression. You can also call it a stamping die, or even use it as a tablet die.
Compression molds can be used for thermosetting plastics, thermoplastics and rubber materials. In other words, the mold material is plasticized and flows to fill the cavity, and then the resin is cured. Therefore, the pressure in the compression molding process is higher than other processes, which belongs to high-pressure forming. Die is also widely used in agriculture, transportation, electric power, chemical industry, construction, machinery and other fields. Based on our many years of experience, DEYING has better control of the molding temperature, material spreading method and the key method of producing high-quality compression molds.
We are responsible for the final molded products and are committed to creating high-precision products that meet customer requirements. The use of reinforced and hardened mold steel and precise processing technology can effectively prevent the product from sticking to the mold and ensure the product's performance and high-quality surface. DEYING's processing method can effectively improve production efficiency and extend mold life. Our team can effectively anticipate possible problems during the design stage and deal with them effectively, and we will do our best to deal with after-sales.
Advantages of the Compression Molding Process
Disadvantages of compression molding process
MB/Wechat/Whatsapp:+0086-13456489912
sophiemould@foxmail.com
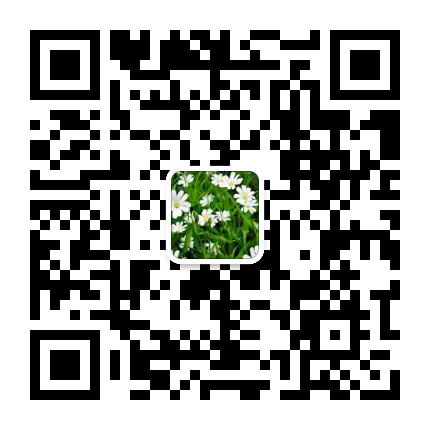
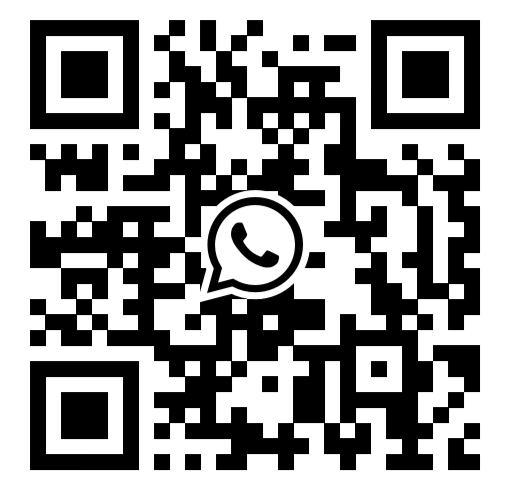
Post time: Jul-23-2021