Compression moulding normally uses a hydraulic press in which a moulding tool is fixed to top and bottom platens of the press. The moulding tool consists of a top cavity and bottom cavity, designed to produce the part to be manufactured and heated to the required moulding temperature. Once the materials of choice are placed into the open mould, the press closes to apply an agreed pressure designed to force the material to flow within the cavities of the mould. The moulding cycle continues to maintain heat and pressure until the polymer has cured and the part moulded. Once moulded it is removed from the tool and trimmed to provide a finished part.
Compression moulding is often associated with Sheet Moulding Compound (known as SMC), Bulk Moulding Compound (known as BMC) and Long Glass Fibre Polypropylene (known as LGFP). The materials all use long glass fibre as its reinforcement and have been formulated to meet specific performance levels required for the part to be produced. They are ideal replacements for metal, aluminium, concrete and timber components.
A high-pressure moulding process, compression moulding produces high strength, lightweight and complex parts in a variety of sizes. The tooling utilises matched metal moulds which are mounted in a hydraulic or mechanical moulding press and the material of choice is placed by robotics or hand in the open mould. The heated moulds once closed, apply pressure between 7 and 20 MPa. This will be based on the materials chosen and the part to be produced. Cycle time will also depend on part size, design and thickness, and ranges from one to five minutes. Features such as ribs, bosses, inserts and attachments can also be moulded using this technology.
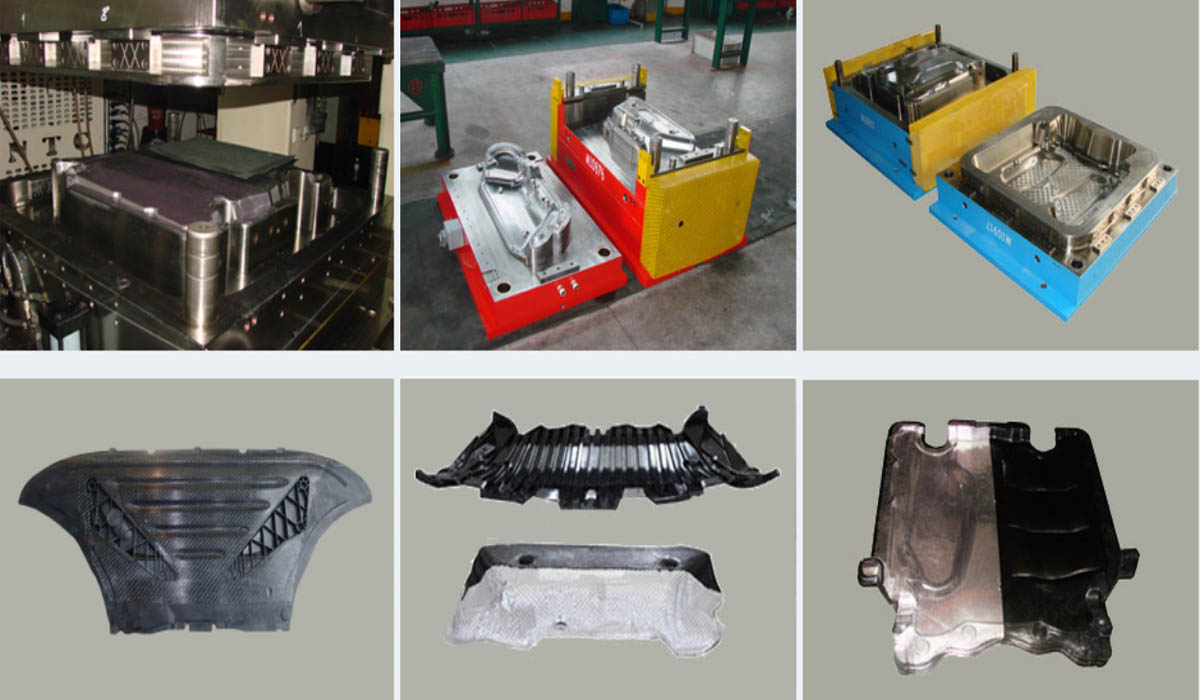
The Pros and Cons of Compression Molding
Let’s take a deeper look at the unique benefits and limitations of this manufacturing process.
Cost-Effective
Compression molding is often the most cost-effective manufacturing method if you need to produce simple, mostly flat, large parts. Some curves and pockets in designs are acceptable, but extreme angles and deep draws can be challenging to achieve through compression molding. Due to the lower pressures, tooling costs are affordable, and molds typically last a long time without warping or needing to be replaced. To offset the cost associated with compression molding’s long cycle times, manufacturers can use a mold with multiple cavities to produce multiple parts in the same cycle.
Produces Strong Parts
Compression molding produces solid parts that are free of flow and knit lines. The structural stability of compression molded parts is very high. Compression molding is also used to manufacture parts using composite materials, which means that durable, corrosion-resistant parts and products can be produced easily through this method.
Flexibility in Design
Compression molding is also a great manufacturing tool for engineers and product developers. For example, prototyping can be done using low-cost compression molding. Simple compression molds can be designed in computer-aided design (CAD) software, 3D printed, and then used to form various types of materials with a simple tabletop vise. You’ll find an example of how DEYING does prototyping this later on in this article.
Limitations
While there are many benefits to using compression molding, it does have its limitations. Compression molding doesn’t work well for manufacturing complex parts, such as those with severely slanted angles or small details. The cycle time, which can be several minutes long, is slow in comparison to high-volume molding methods. Injection molding, for example, often has cycle times of just seconds.
The labor cost associated with compression molding can be relatively high as well due to the slow cycle time that correlates with more working hours. Flash and burrs need to be manually removed from compression-molded parts, which takes up more time and creates waste. All these limitations aside, compression molding is still an important manufacturing method that is used to produce a wide range of products that we use every day.
MB/Wechat/Whatsapp:+0086-13456489912
sophiemould@foxmail.com
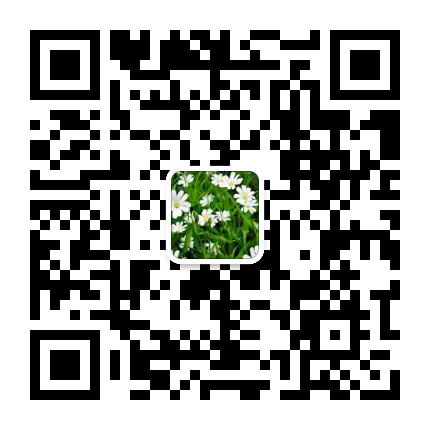
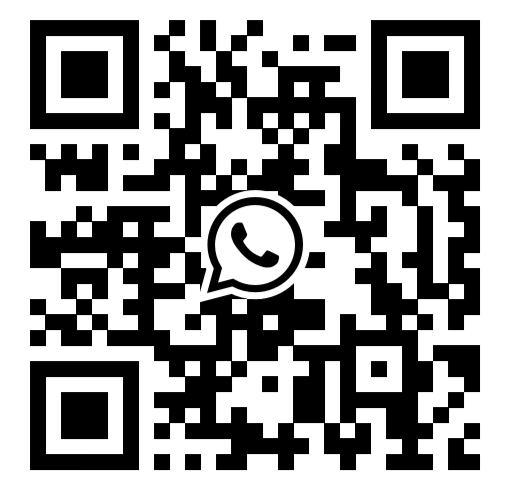
Post time: Jul-11-2021