Manufacturing Kevlar bulletproof helmet mold
UHMWPE is commonly known as ultra-high molecular weight polyethylene. Its molecular weight can reach 1 to 5 million. It has high wear resistance, low friction coefficient, highest impact resistance, and excellent sound-absorbing performance. Compared with ordinary thermoplastics, it has extremely low fluidity and is extremely difficult to process. At present, it can only be produced by molding. Our company cooperates with military industry units to use its excellent impact resistance to develop body armor and bullet-proof helmet molds, realize segmented pressurization and heating on a pair of molds, and switch the heating mold to the cooling mold in the final stage of molding to ensure The product is cooled and shaped to the set temperature and set material hardness to ensure that the product can be easily taken out of the mold
lassification of compression molding die
1. Compression molding
Put the SMC sheet and BMC mass into the heated mold. After the mold is closed, the material fills the entire cavity and polymerizes. After the product is completely cured, the product is ejected from the mold.
2. Transfer molding
Place the prefabricated SMC or BMC on the injection valve port, and inject the material into the cavity after closing the mold. The material will fill the entire cavity and polymerize. After being completely cured, the hot product is demolded and made.Transfer molding is suitable for those multi-cavity molds that require high strength of thin-walled products.
3. Injection molding
Put the BMC or injection-molded SMC on the filler that feeds the injection device. These thermosetting materials require check valves. The composite material is then injected into the closed mold to fill the cavity and polymerize. After being completely cured, the hot product is demolded and made.Injection molding is used for the processing of high-precision parts and complex bodies.
4. Injection-compression molding
Put the BMC or injection-molded SMC on the filler that feeds the injection device. These thermosetting materials require check valves. The composite material is then injected into a half-fit mold, fills the cavity and polymerizes. After being completely cured, the hot product is demolded and made.Injection-compression molding can maintain glass fiber and improve cavity exhaust. This processing is suitable for products with high mechanical strength.
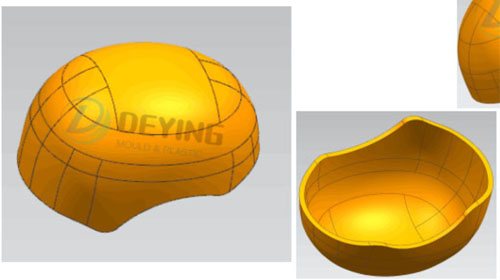
Other thermosetting plastic molds
In addition to SMC, BMC, and DMC, the following composite materials are usually used in compression molding and transfer molding processes:
1. Phenolic resin (PF)
2. Amino resin
3. Epoxy resin (EP)
4. DAP resin
In addition to the commonly used molding processes for SMC and BMC press molding, the following molding processes are also used:
1. Molding plastic injection process:
Put the BMC or injection-molded SMC on the filler that feeds the injection device. These thermosetting materials require check valves. The composite material is then injected into the closed mold to fill the cavity and polymerize. After thorough curing, the hot product is released from the mold. The injection molding process is used for the processing of high-precision parts and complex bodies.
2. Injection molding-compression molding
Put the BMC or injection-molded SMC on the filler that feeds the injection device. These thermosetting materials require check valves. The composite material is then injected into a half-fit mold, fills the cavity and polymerizes. After thorough curing, the hot product is released from the mold. Injection-compression molding can maintain glass fiber and improve cavity exhaust. This processing is suitable for products with high mechanical strength.
Post time: Aug-09-2020