There are many types of spinnerets, and the spinnerets used to make non-woven fabrics for masks are just one of them. Below, Shengshuo Precision Machinery organizes the main types of spinnerets on the market for you.
(1) Spinneret for wet spinning
Spinnerets for French spinning are mainly used in the manufacture of high-end women's clothing such as bedding, dresses and blouses, and cigarette filters. With the tools independently developed by our company, it is possible to punch out regular triangular holes and round holes with a side length of 0.030~0.0150mm.
(2) Dry spinning method spinneret
The dry spinning method is a spinning method in which the resin is dissolved in a solvent, and then extruded through the small holes of the spinneret, and the solvent is vaporized by hot air to become a fiber.
(3) Spinneret for melt spinning
The spinneret for melt spinning is a representative spinneret for the production of synthetic fibers such as polyester and nylon.
In addition, through self-made tools and unique processing technology, the surface processing accuracy can be selected from mirror processing, grinding (pear surface) processing, and super mirror processing.
A spinning method in which thermoplastic resin is heated and melted, extruded through a spinneret in air or water at a certain speed, and cooled and solidified into fibers.
(4) Dry and wet spinning method spinneret
The dry-wet spinning method is suitable for the manufacture of acrylic fiber and aramid fiber. Using the spinning technology of tow densification, high-strength, high-elastic fibers can be produced.
The dry-wet spinning method is a spinning method in which the resin extruded from the spinneret travels in the atmosphere and immediately enters the coagulation liquid to coagulate into fibers.
(5) Spinneret for composite spinning
By combining the raw materials, the production of high-performance fibers that cannot be produced with a single type of resin, such as ultra-fine fibers, conductive fibers, etc., is realized.
The spinneret assembly for composite spinning has high technical requirements for the position coordination, temperature control, and flow path design of the upper parts.
The composite spinning method is a fiber manufacturing method in which two or more different resins are spun from one hole at the same time, and the characteristics of each resin are utilized.
(6) Water needle board
The spunlace method is a reinforcement method that uses high-speed water flow to impact the fibers to encourage the fibers to entangle and hug each other, so as to achieve a certain strength of the cloth surface. The non-woven fabric made by this method is also called "water-wrapped non-woven fabric", which is widely used in wet wipes, cosmetics, surgical gowns and other materials.
The long jet of column-shaped water stream improves high-performance winding, which can reduce processing loss and water flow dispersion, and achieve energy-saving effects.
(7) Spinnerets and die heads for non-woven fabrics
Spinneret for spunbonding
Spunbond non-woven fabric is a kind of non-woven fabric formed by melting resin with low melting temperature and polymerizing it into a net through spinneret drawing. It has the characteristics of lightness, softness and sturdiness and diversified production types.
Melt blown cloth spinneret
Melt-blown non-woven fabric is a non-woven fabric formed by using high-speed hot air flow to draft the fiber extruded from the spinneret and entangle the fiber. Non-woven fabrics used in masks and industrial filter elements can be manufactured from raw resin to the first stage.
(8) Spinneret for hollow fiber
Hollow fiber forming molds, hollow fibers for artificial dialysis, and hollow fiber spinnerets for filtration, can be designed into single and multiple types, as well as triple tube types.
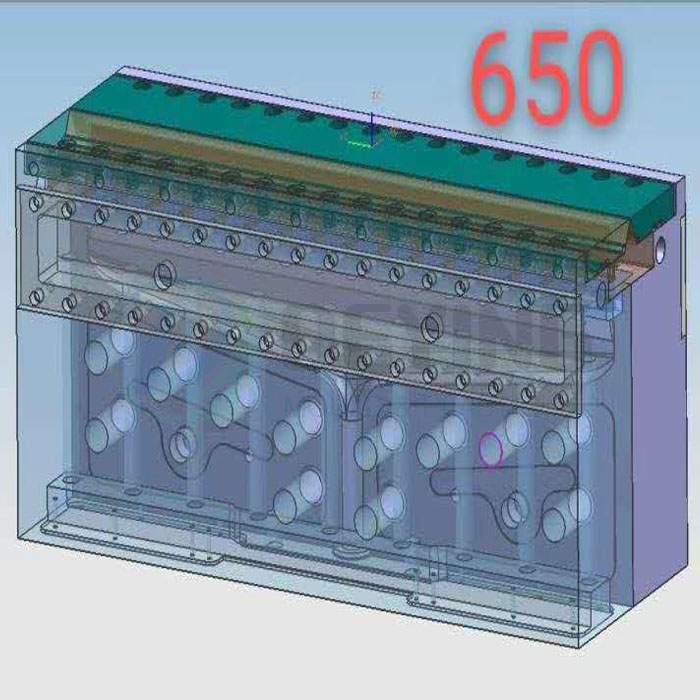
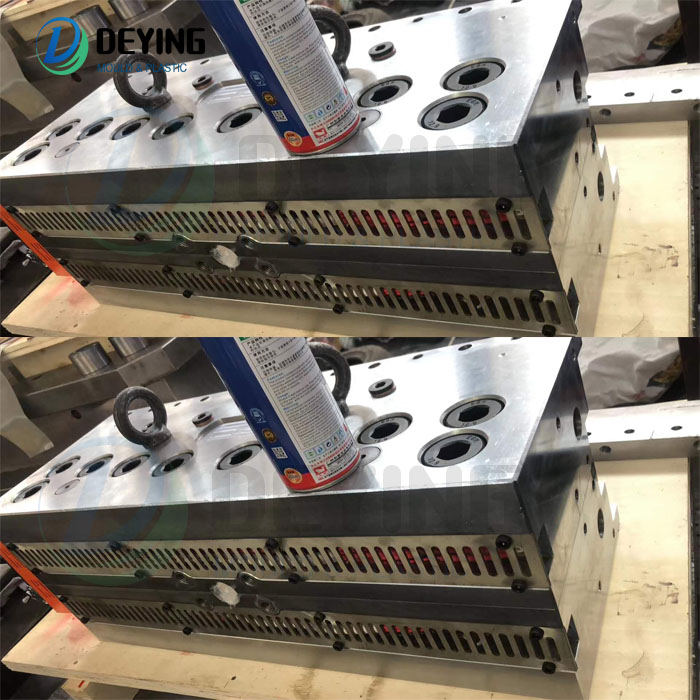
Spinneret maintenance introduction Spinneret maintenance introduction
The spinneret will reduce the quality of the product after many years of use and wear. Repairing, inspecting or optimizing the spinneret will restore the spinneret to an almost new state.
Spinneret
1. Regular maintenance (grinding/polishing the surface of the spinneret, recalibrating the pores);
2. Repair damaged capillaries or spinning plates;
3. Modify and optimize the spinneret, increase or block the spinneret hole;
After maintenance, the spinneret can be put into a new round of use.
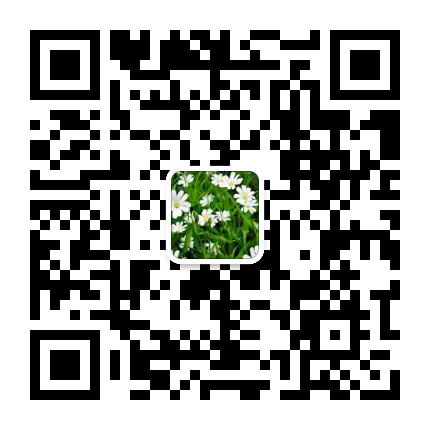
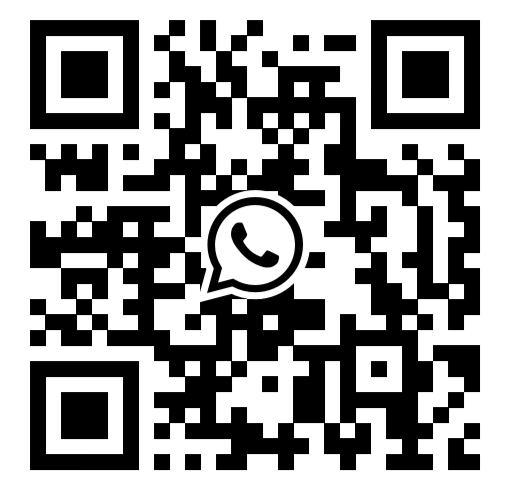
MB/Wechat/Whatsapp:+0086-13456489912
sophiemould@foxmail.com
Post time: May-27-2021