At present, my country's rubber products industry is developing rapidly, the types of rubber products are increasing day by day, and the output is also increasing day by day. With the continuous improvement of rubber production equipment and production technology, the design and manufacture of rubber molds have been transformed from traditional empirical design to theoretical calculation design, and the manufacturing level and complexity of molds are getting higher and higher, and they are gradually moving towards automatic and efficient. With the development of high precision and long service life, let’s talk about the types of rubber molds below?
Rubber molds are divided into four commonly used molds according to the mold structure and product production process: compression molding molds, die-casting molding molds, injection molding molds, and extrusion molding molds, as well as some special rubber molds for producing special rubber products, such as inflatable molds, Dipping molds, etc.
Commonly used rubber product molds are as follows:
1. Extrusion mould
The semi-finished rubber profiles of various cross-sectional shapes are made by the molding die of the machine head to achieve the purpose of preliminary modeling, and then are cooled and shaped and transported to the vulcanizing tank for vulcanization or used as the pre-formed semi-finished rubber material required by the compression molding method.
2. Compression molding Mould die
Also known as ordinary compression mold. It puts the mixed, processed into a certain shape and weighed semi-finished rubber material directly into the mold, and then sends it to the plate vulcanizer for pressure and heating. The rubber material is vulcanized and formed under pressure and heating.
Features: The mold has simple structure, strong versatility, wide range of use, and convenient operation, so it occupies a large proportion of rubber molded products.
3. Die casting mould
Also known as transfer mold or extrusion mold. It is to put the mixed, simple shape, a certain limited amount of semi-finished rubber or rubber block into the die-casting mold cavity, squeeze the rubber through the pressure of the die-casting plug, and make the rubber enter the mold cavity through the pouring system Middle vulcanization stereotypes.
Features: It is more complex than ordinary compression molds, and is suitable for making thin-walled, slender and flexible products that cannot be compressed or barely compressed by ordinary compression molding, as well as rubber products with complex shapes and difficult to feed. Using this mold 4, injection molding mold
It is to inject the rubber material preheated into a plastic state into the mold through the pouring system of the injection mold to shape and vulcanize.
Features: complex structure, suitable for large-scale, thick-walled, thin-walled, and complex-shaped products. The production efficiency is high, the quality is stable, and the automatic production can be realized.
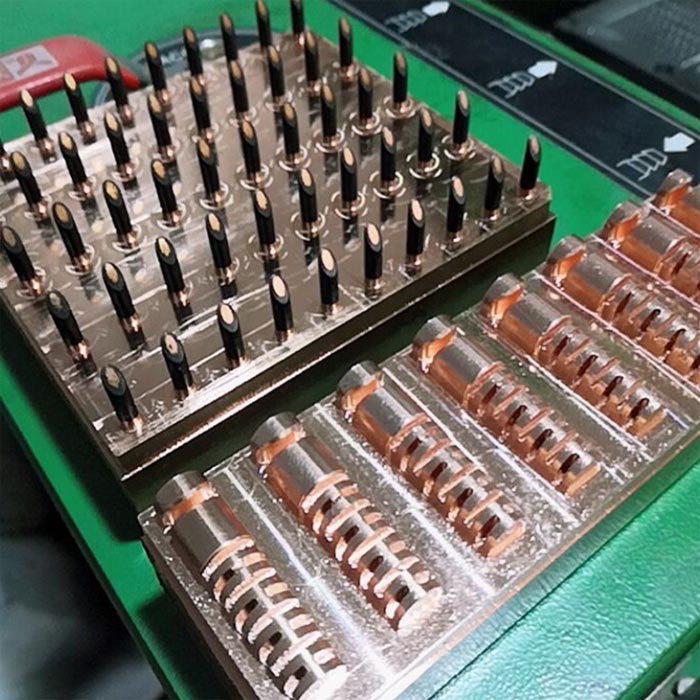
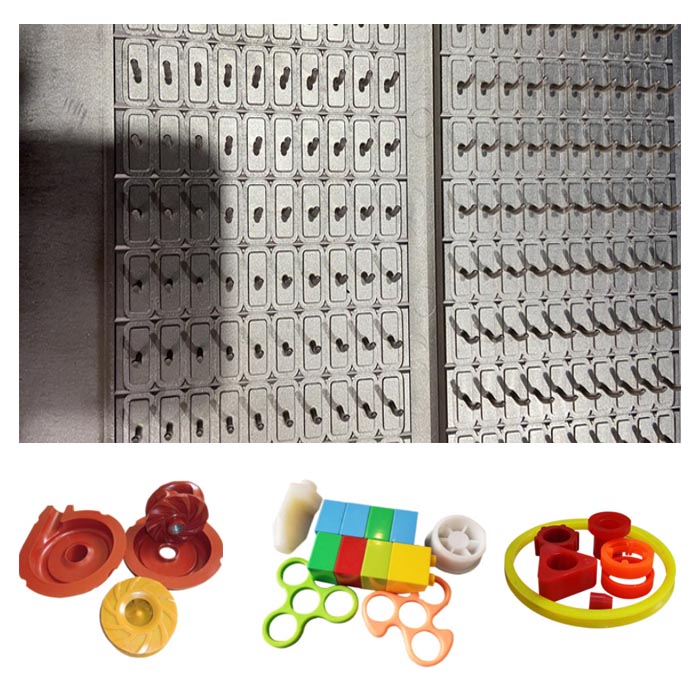
MB/Wechat/Whatsapp:+0086-13456489912
sophiemould@foxmail.com
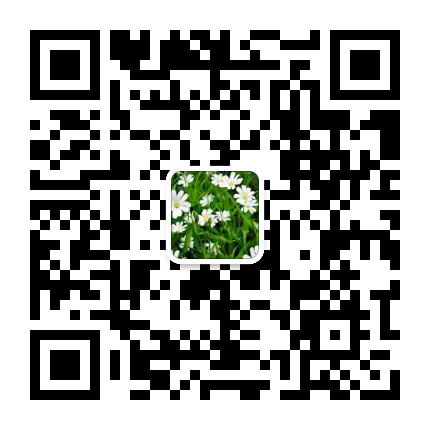
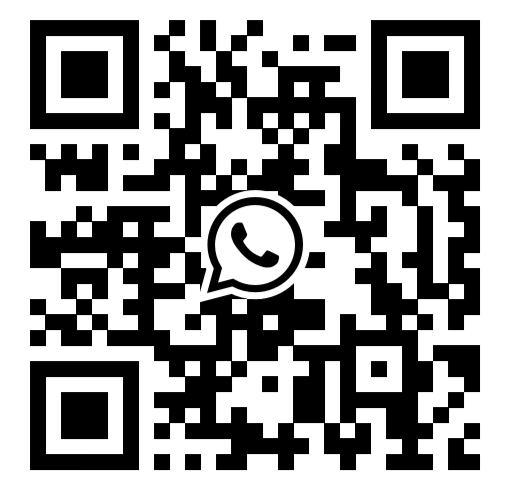
Post time: Dec-18-2021