Many parts are made of carbon fiber compression molds, such as some parts of automobiles
Fiber is a polymer, also known as graphite fiber, because it is made of organic fibers such as flake graphite crystallites stacked along the axial direction of the fiber. It is a microcrystalline graphite material obtained by carbonization and graphitization. Very sturdy and very light at the same time. Compared with steel, carbon fiber is not only five times stronger than steel, but also twice as rigid as steel, and it is much lighter than steel. Make it an ideal manufacturing material for many parts. These are just a few reasons why carbon fiber is favored by engineers and designers in manufacturing.
Carbon fiber is thinner than human hair, and when entangled like yarn, carbon fiber can increase its strength. Therefore, it can be woven together to form a cloth. If a permanent shape is required, only the carbon fiber is laid on the mold, and then the simple process of coating with resin or plastic is completed.
Because carbon fiber has high rigidity, high tensile strength, low weight-to-strength ratio, high chemical resistance, high temperature resistance, and low thermal expansion rate, carbon fiber is very popular in many industries such as aerospace, automotive, military and entertainment applications.
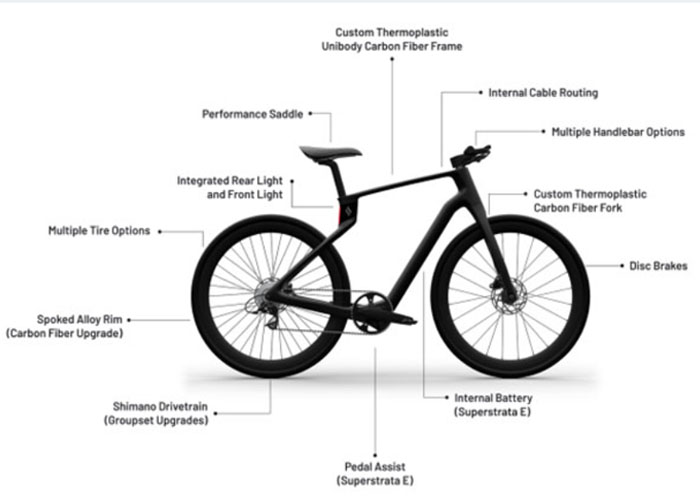
A brief history of carbon fiber:
The history of carbon fiber can be traced back to 1879. The British Swann first used carbon filament to make the filament of an electric light bulb. Later, Thomas Edison baked cotton thread or bamboo silver at high temperature and then carbonized it into full carbon fiber filament. A practical incandescent lamp carbon filament was developed. However, due to the invention of the method of drawing tungsten filament by Culich in 1910, the filament was completely changed to tungsten filament, and the early carbon fiber research was broken into the cold palace. By 1958, high-performance carbon fiber was invented outside of Cleveland, Ohio. Although these fibers are inefficient, they contain about 20% carbon and have low strength and stiffness properties. In 1963, a new manufacturing process was developed in a research center in the UK, where the strength potential of carbon fiber was realized. After the 1950s, in order to solve the problems of high temperature resistance and corrosion resistance of missile nozzles and warheads, the United States developed viscose-based carbon fibers. Although it has been developed for a long time, the technology in the civilian field is still immature. The manufacturing cost of truly high-strength carbon fiber remains high, which makes it extremely difficult to promote.
Overview of carbon fiber manufacturing process:
Carbon fiber is made by a partly chemical and partly mechanical process. First, the long bundle of fibers is stretched, and then heated to a high temperature, while not allowing contact with oxygen to prevent the fibers from burning. This is the time when carbonization occurs, that is, the atoms inside the fiber vibrate violently, and most of the non-carbon atoms are expelled. This leaves fibers composed of long and tightly interlocked chains of carbon atoms, leaving only a few non-carbon atoms.
The typical steps for forming carbon fibers from polyacrylonitrile include spinning, stabilization, carbonization, surface treatment and sizing.
What can carbon fiber do?
Because carbon fiber is a lightweight substitute for many materials, carbon fiber can replace almost all products, such as bicycle frames, airplane wings, automobile transmission shafts, pipes, containers, propeller blades, auto parts, sports equipment, etc.
Carbon fiber currently has a significant effect in automobile manufacturing. Carbon fiber composite materials can reduce the weight of passenger cars by 50%, which will increase fuel efficiency by nearly 35% without affecting the performance of the car or the safety of the occupants. This is another milestone in the history of vehicle manufacturing.
MB/Wechat/Whatsapp:+0086-13456489912
sophiemould@foxmail.com
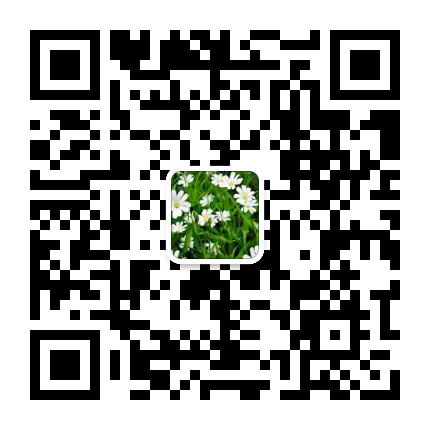
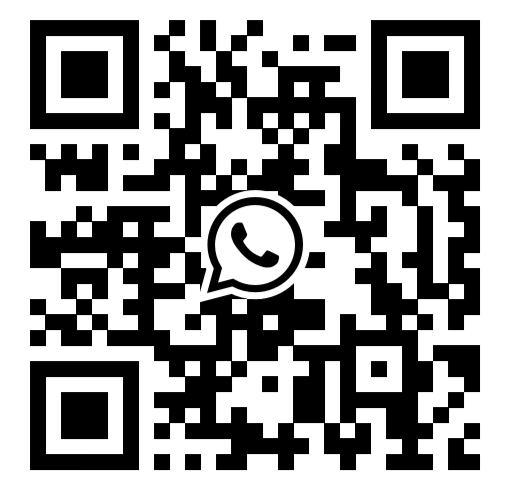
Post time: Aug-13-2021