Deying Mould a professional production Tactical Bulletproof Helmet Moulds factory,has extensive experience in military field's product molds.Whether it is PE or Kevlar materials products, we can provide the perfect solution.
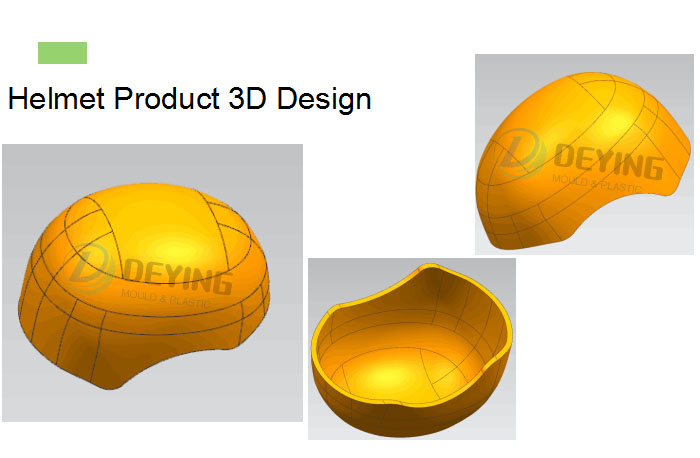
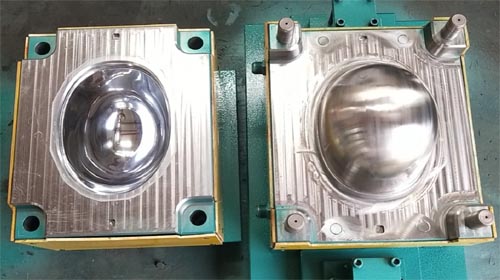
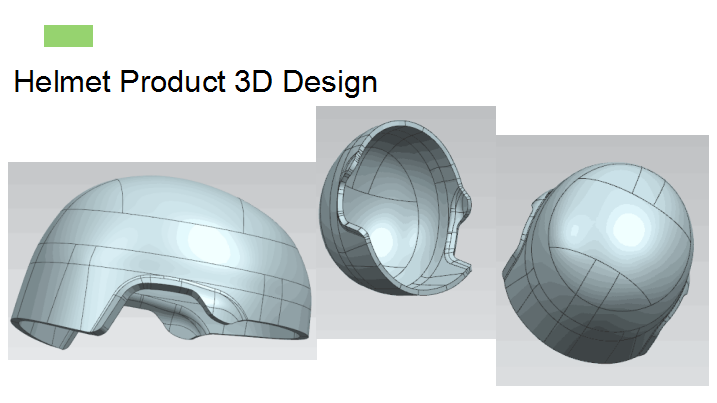
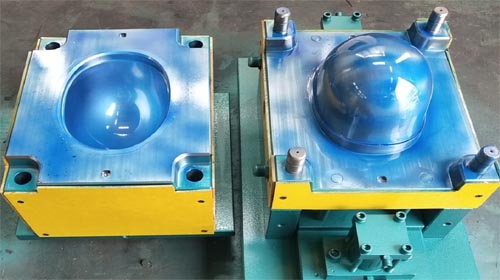
DEYING is one of the earliest manufacturers of FRP composite products in Huangyan, Taizhou. The company’s current main business is carbon fiber composite moulding and thermosetting plastics.
SMC, BMC, DMC, GMT glass fiber reinforced plastic molds and Kevlar bullet-proof helmet molds are mainly companies that integrate mold design, manufacturing, processing, and product suppression. Carbon fiber composite material molding mold covers aerospace aircraft structural parts, unmanned aerial vehicles, advanced sports equipment, etc.; glass fiber reinforced plastic molds include SMC meter boxes, sanitary ware, power building materials, etc. Since 2008, the company has cooperated with military scientific research units and enterprises to develop directional paving material technology and the development and trial production of forming molds. The application of UD/Kevlar bulletproof composite materials in the field of domestic military protective equipment has played a key role in the company. It is currently one of the largest suppliers of Chinese military bulletproof series product molds, and is a manufacturer specializing in the production of glass fiber reinforced plastic product molds in China.
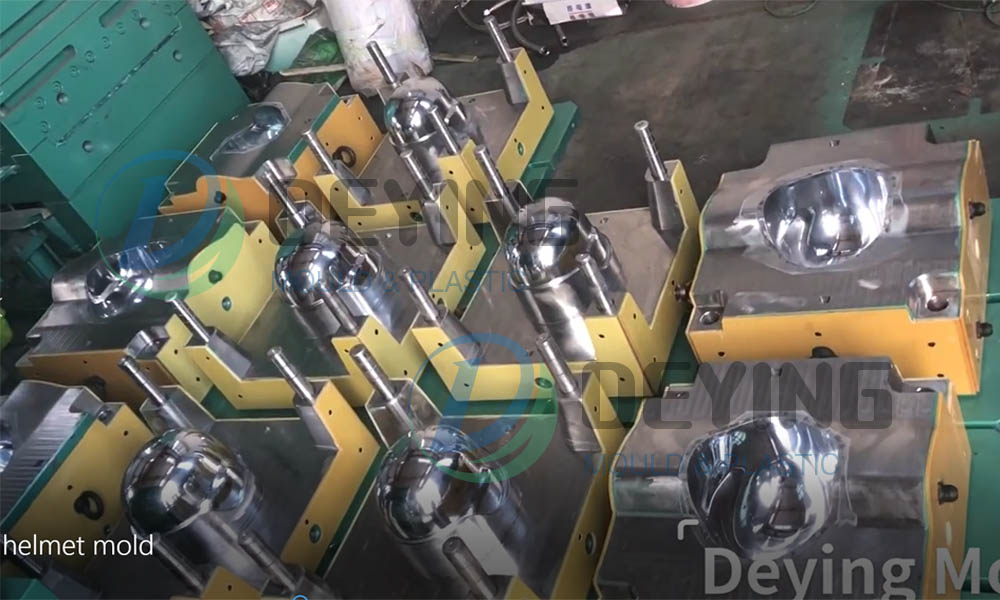
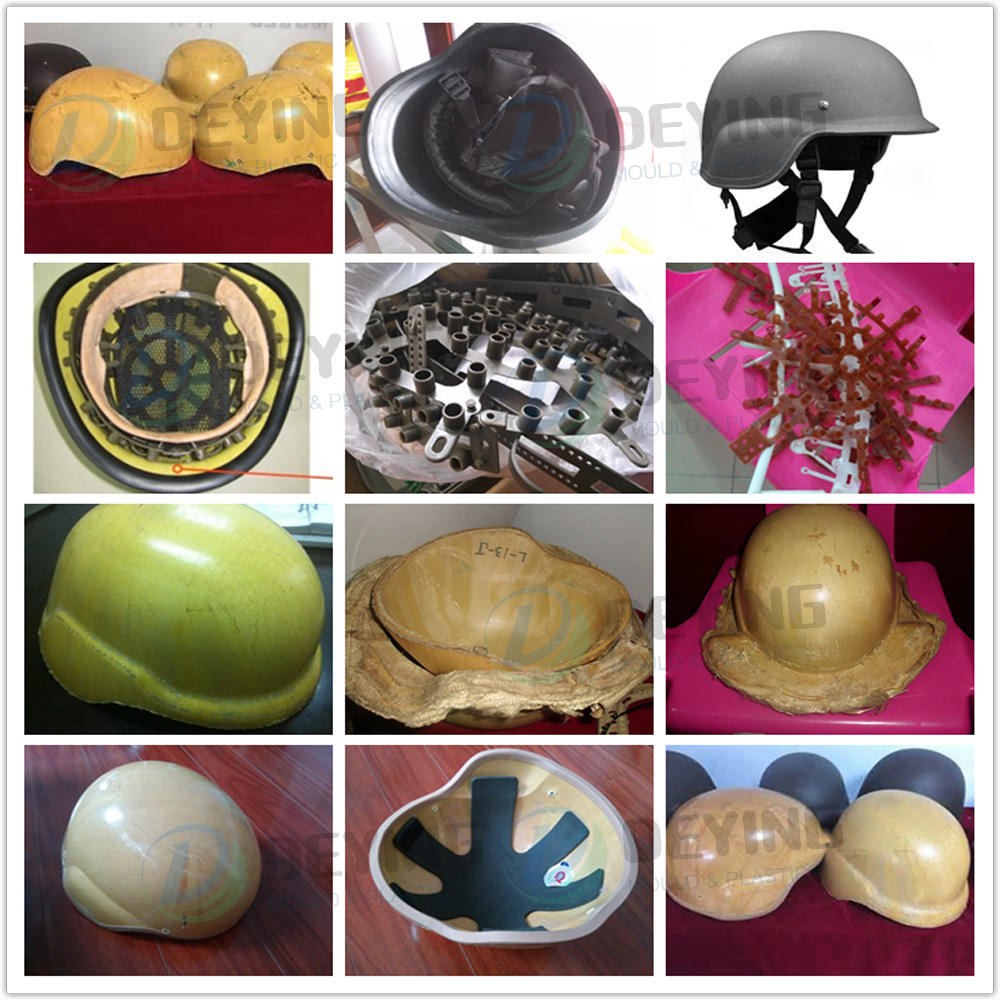
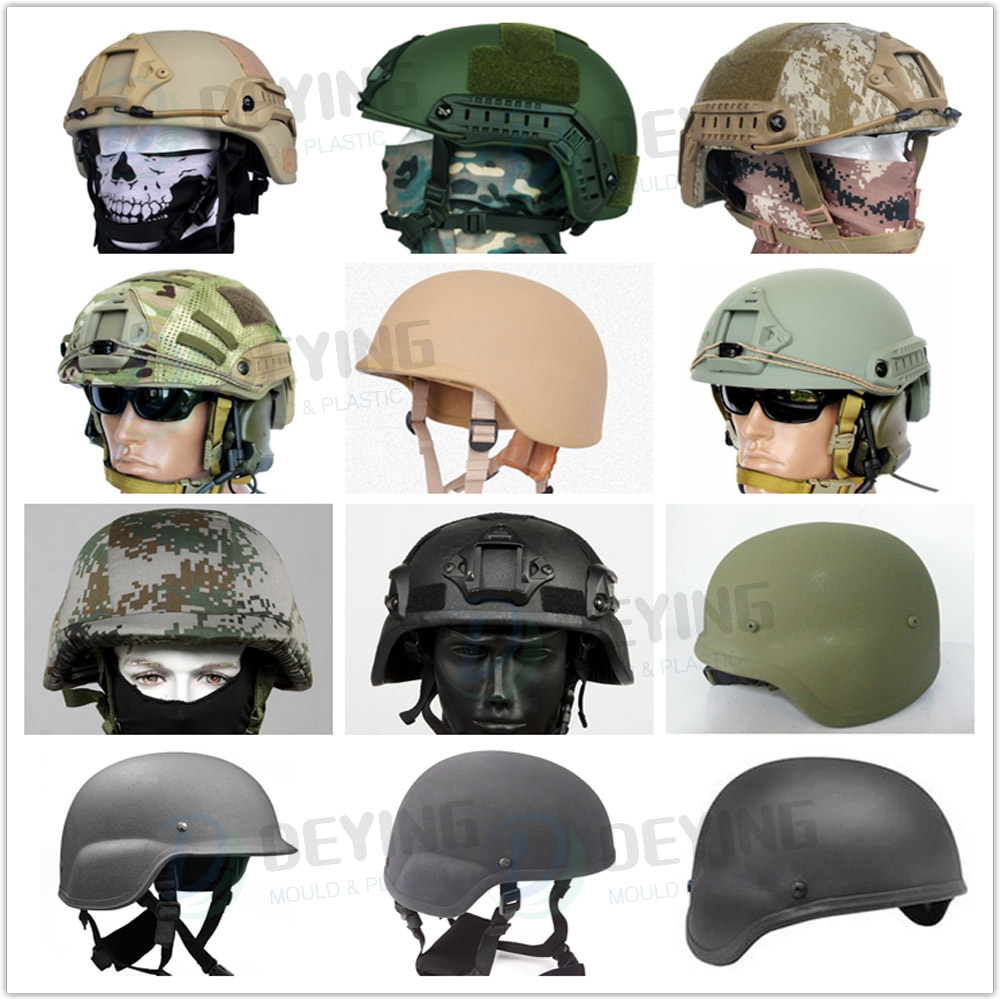
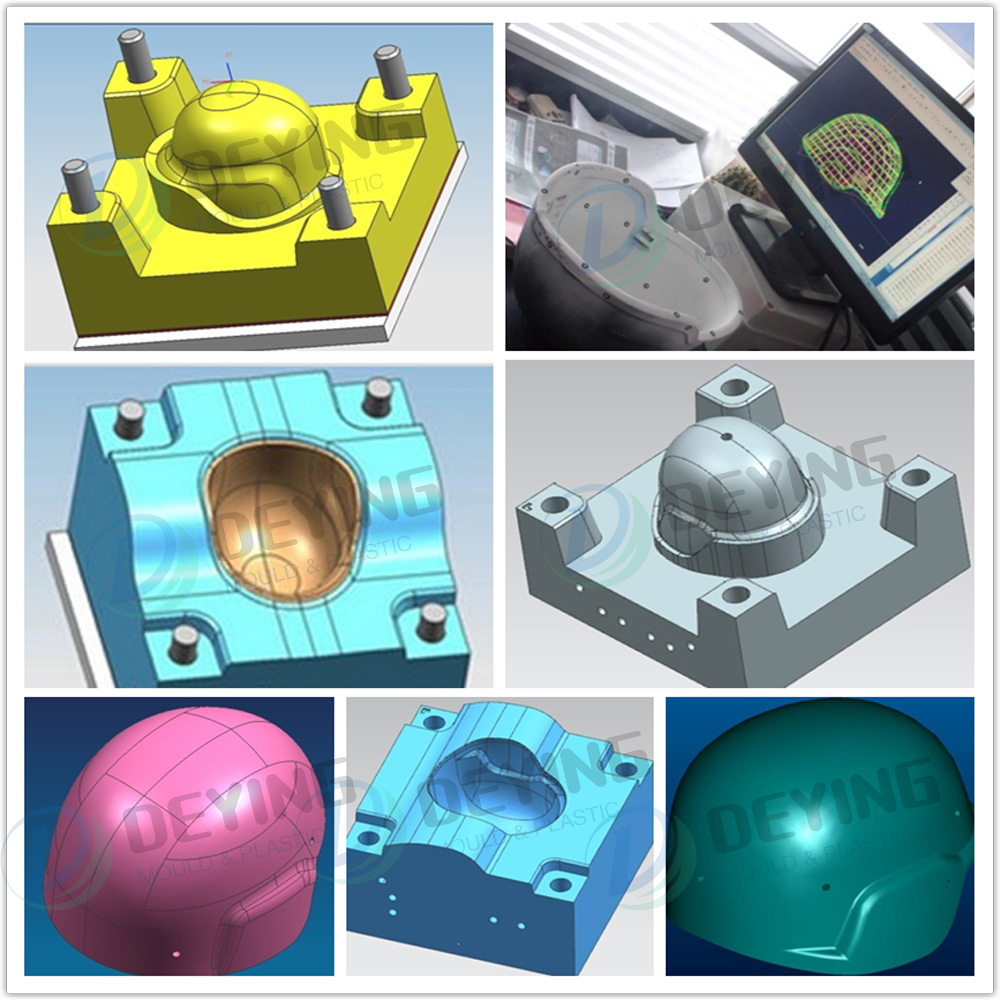
Mold quality control
We have our own complete production and management system, and we have quality control in every production link. Its scope is: from the design structure of plastic products to the feasibility of mold structure design, from mold raw material procurement to raw material inspection, from raw material processing technology selection to part quality inspection, from part assembly to mold overall inspection, mold trial, etc. And other manufacturing processes related to molds.
1. Product design review: Analyze the product structure, product structure, product wall thickness, parting surface selection, draft angle, product appearance and internal view, and determination of important product dimensions.
2. Mold design review: analysis from the mold parting surface, mold core pulling mechanism, casting system, cooling system, manufacturing process, guiding system, mechanical strength of each part of the mold, etc.
3. Arrangement of mold parts processing technology and determination of processing technology parameters
4. In the mold processing process, each component is tested to ensure that each processing step has no defects and flows into the next process, especially the size of the mold parting surface and the matching size of the mold moving parts.
5. Mold assembly process control
6. Mold trial process control
7. Sample test report
8. Correction of customer feedback results
9. Mold installation test
10. Inspection of molds before shipment
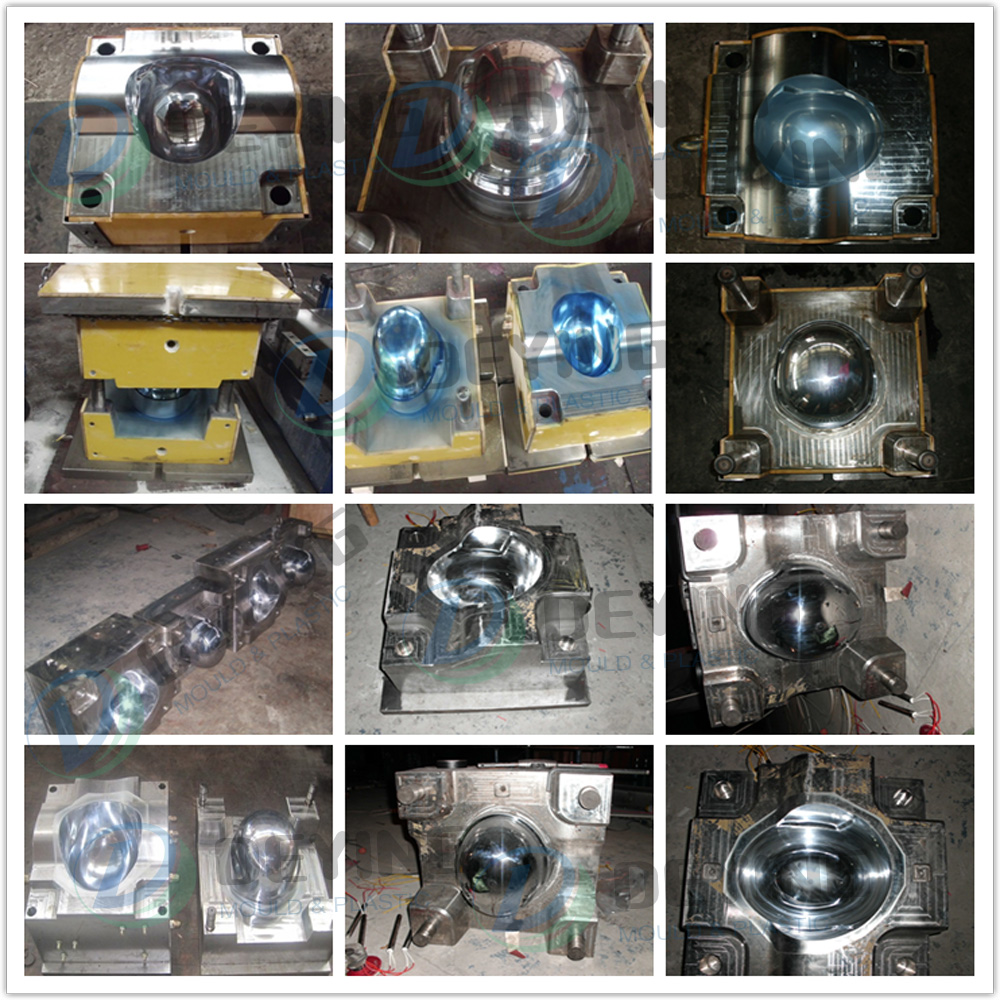
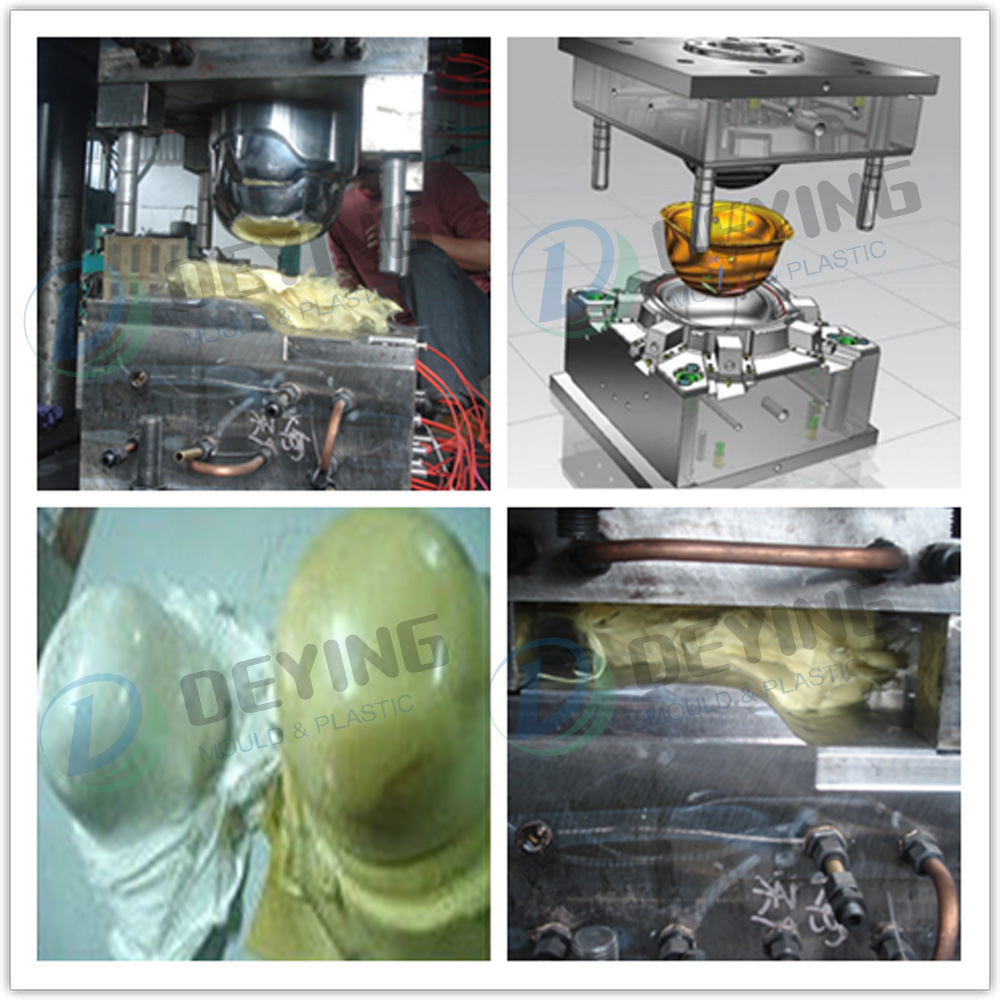
MB/Wechat/Whatsapp:+0086-13456489912
sophiemould@foxmail.com
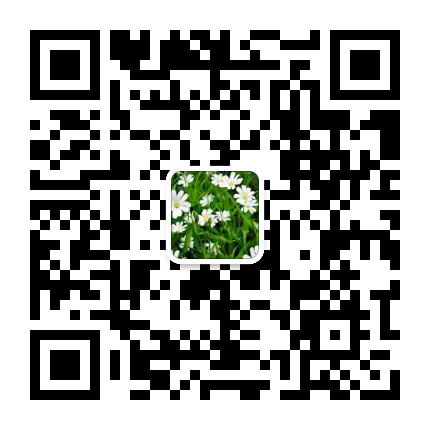
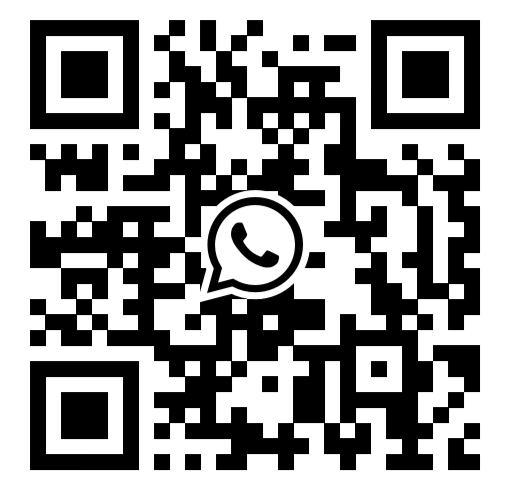