We focus on the development and manufacture of SMC, BMC, GMT and other composite molds, especially FRP compression manhole cover molds. The company uses advanced software such as CAE\CAD\CAM\CAQ to assist mold development and quality control; has advanced CNC machining equipment to ensure the high precision and high quality of the mold; continuously optimizes the process flow and powerful CNC machining capabilities , Scientific project management, greatly shorten the production cycle of molds, and provide a powerful guarantee for the rapid listing of your products.
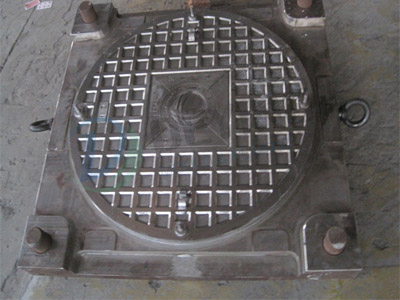
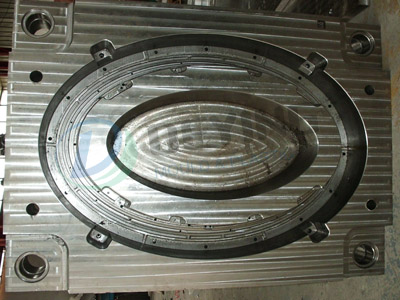
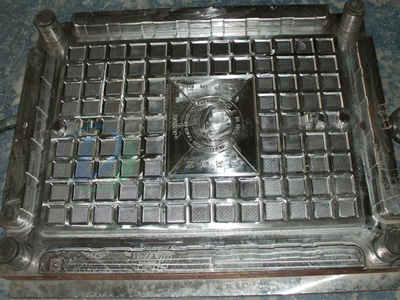
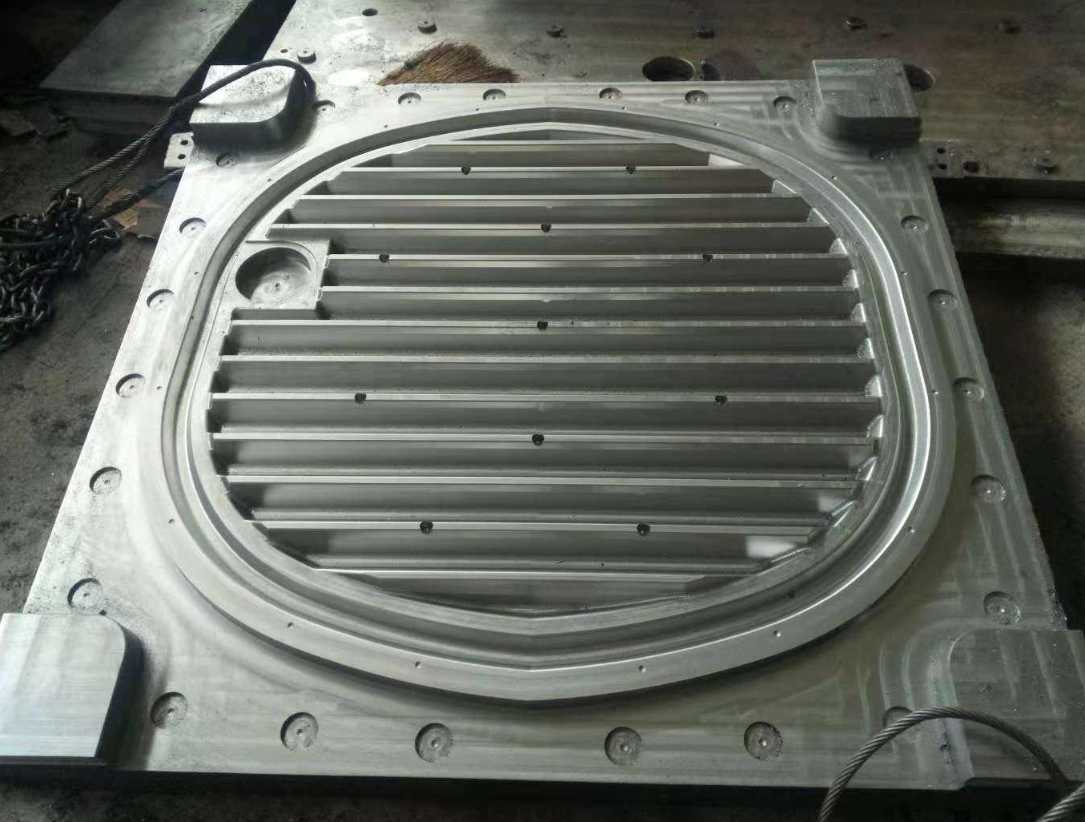
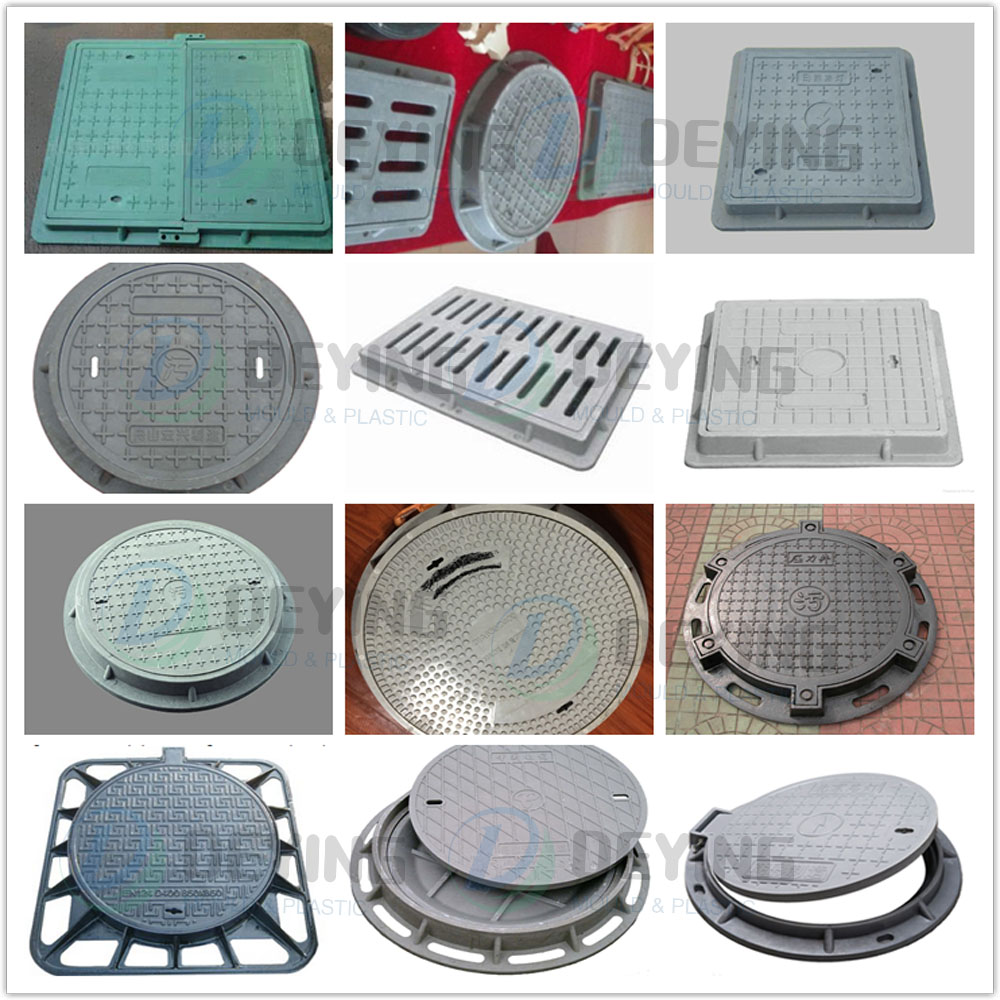
The manhole cover mold of the new composite material is different from the old manhole cover mold. The new product adopts polymer composite material, which is more robust and durable, and has an exquisite appearance, which is conducive to the decoration of the manhole cover and has a great advantage in weight.
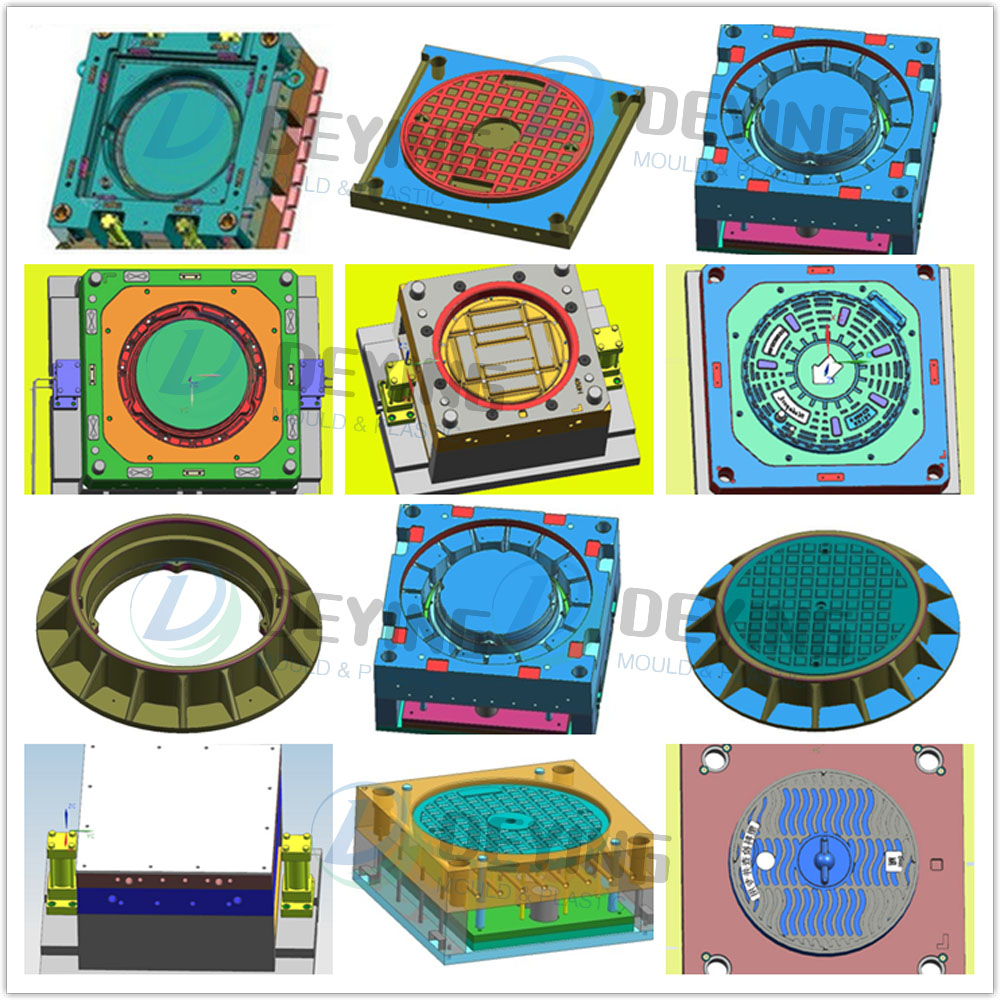
The types of manhole cover molds are: cement round manhole cover mold, county municipal manhole cover mold, inspection manhole cover mold, cement water manhole cover mold
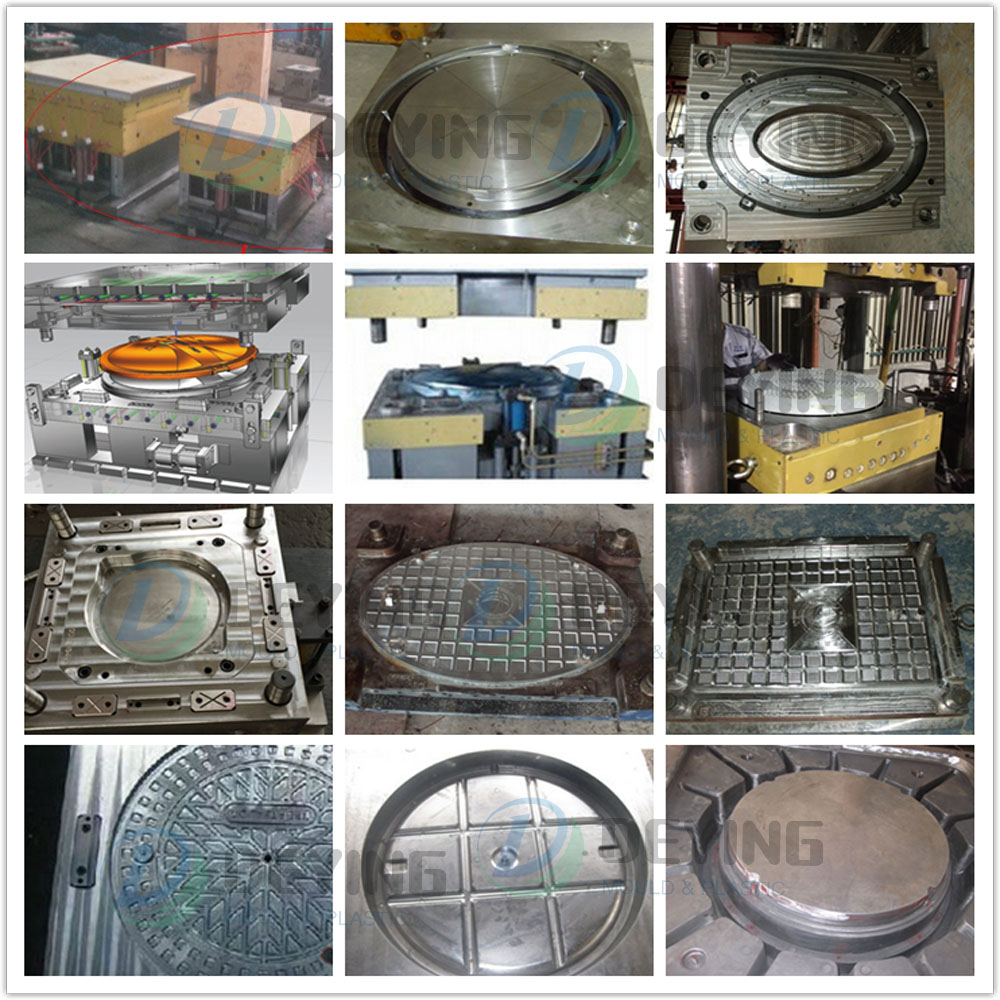
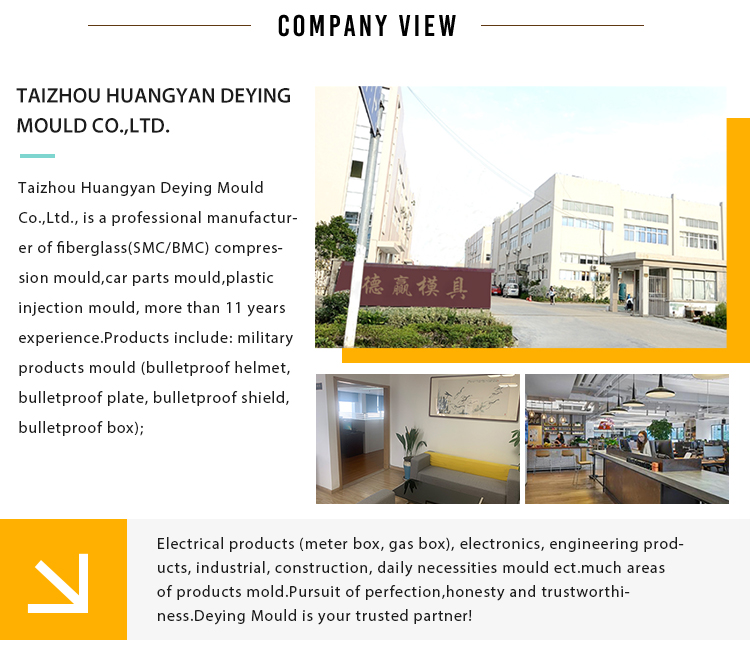
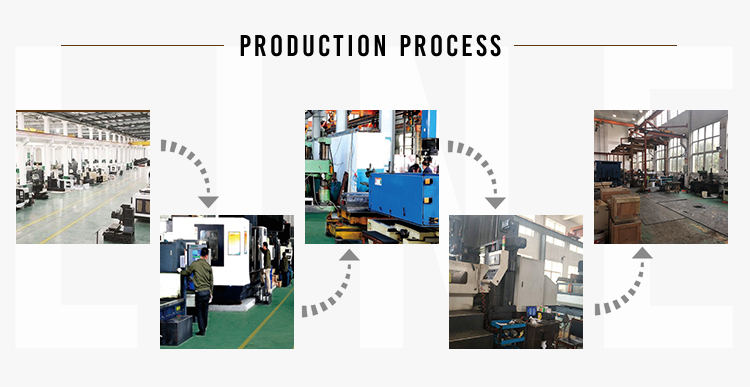
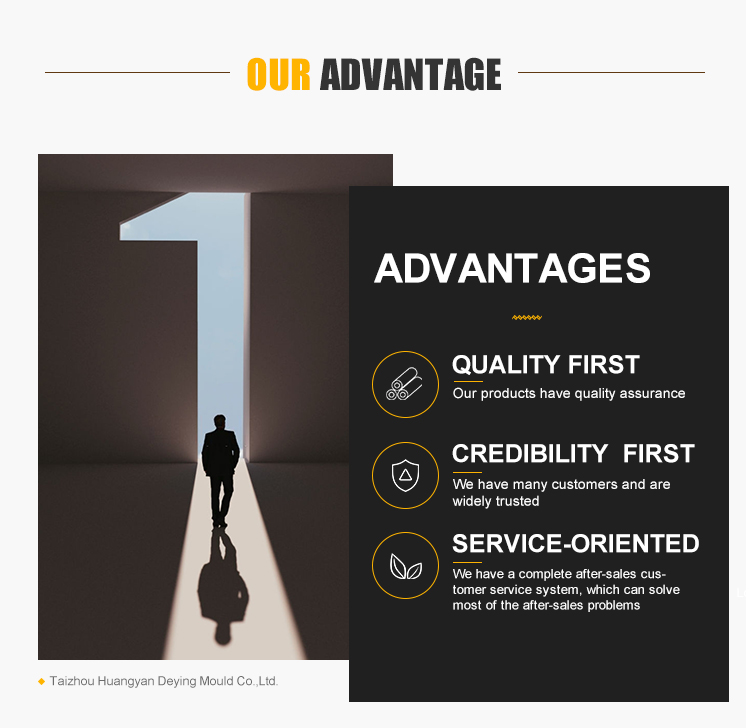
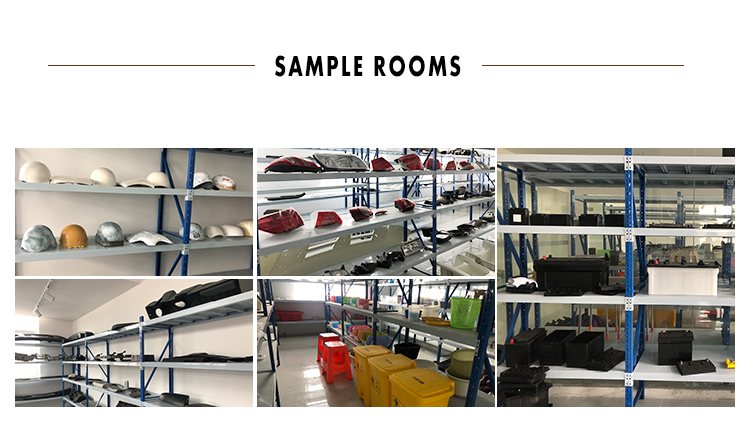
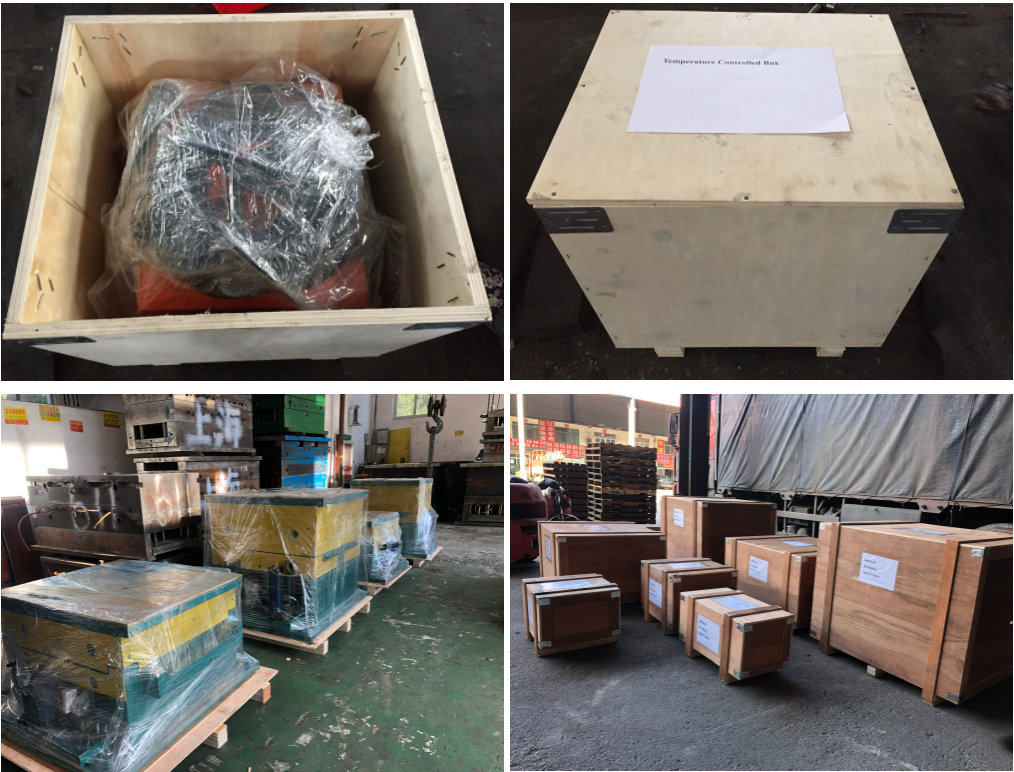
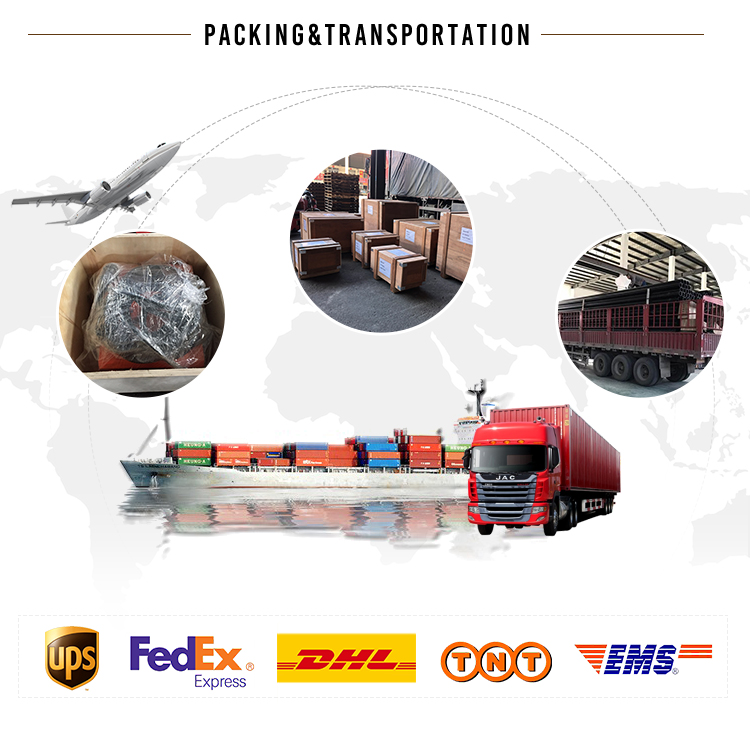
Composite materials are made up of two or more materials with different properties through physical or chemical methods to form materials with new properties. With the broadening of the application field of composite materials, the composite material molding industry has developed rapidly, the old molding process is becoming more and more perfect, and new molding methods are constantly emerging. Commonly used processes include hand lay-up, injection molding, resin injection (RTM), compression molding (BMC, SMC), and vacuum diversion molding processes. To make high-precision composite products, composite molds are an important part of the entire manufacturing process. And the shape and appearance of the product need to be guaranteed by the mold. The composite material mold usually puts the composite material in a hot pressing mold, and then melts the composite material by heating the mold. The mold is equipped with an ejection mechanism to eject the molded product and release it from the mold. Common heating methods for molds include: oil heating, electric heating, steam heating, etc. MDC has many years of experience in manufacturing composite material molds. The molds that have been manufactured include: spoiler templates, mudguards, bumpers, front panel molds on trucks, hoods, doors, bottom guards, roofs, and seats on cars. Chair backrests, luggage box molds, etc., as well as electrical box and bathroom door panel basin molds, etc. The composite molds we produce have been effectively optimized, have a longer service life, lower manufacturing costs, and their products can achieve higher precision.
MB/Wechat/Whatsapp:+0086-13456489912
sophiemould@foxmail.com
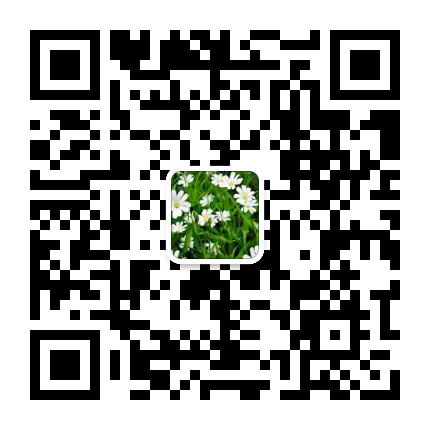
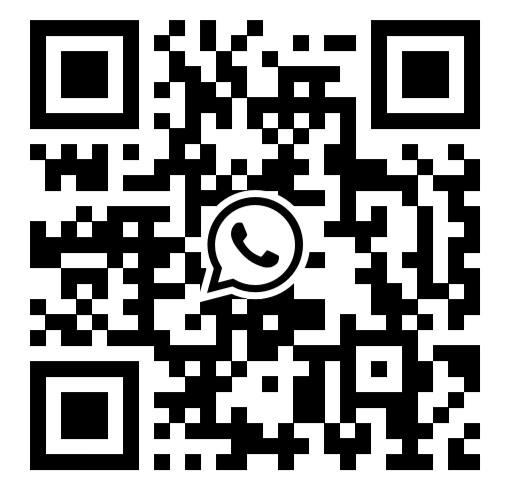