The structure of Vulcanized Silicone Rubber Parts molds are unfavorable. When designing rubber products, attention should be paid to its shape, thickness, and draft angle, among which the draft angle is the main factor. After the product is out of the furnace, the product cools and produces centripetal shrinkage, which produces a large holding force on the core or pin, thereby hindering the demolding. If the demolding slope is increased, this resistance can be significantly reduced, and defects such as tearing of the product due to no slope can also be avoided.
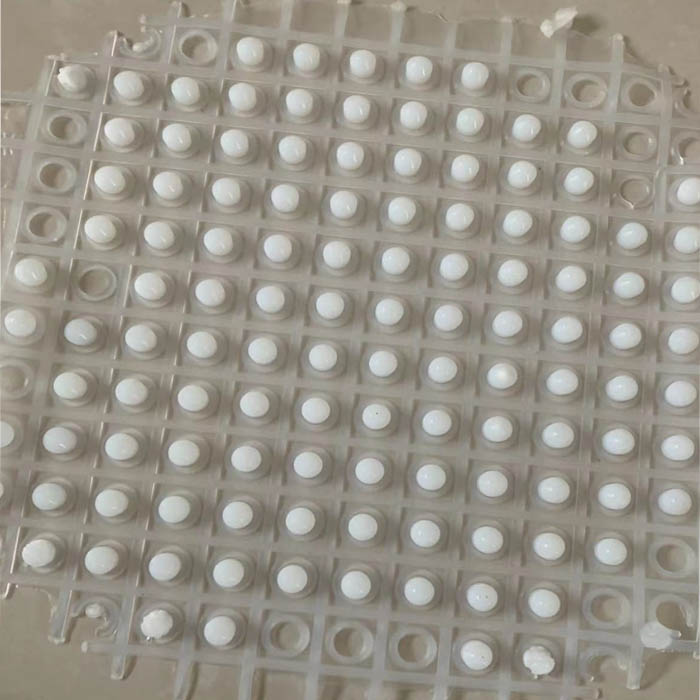
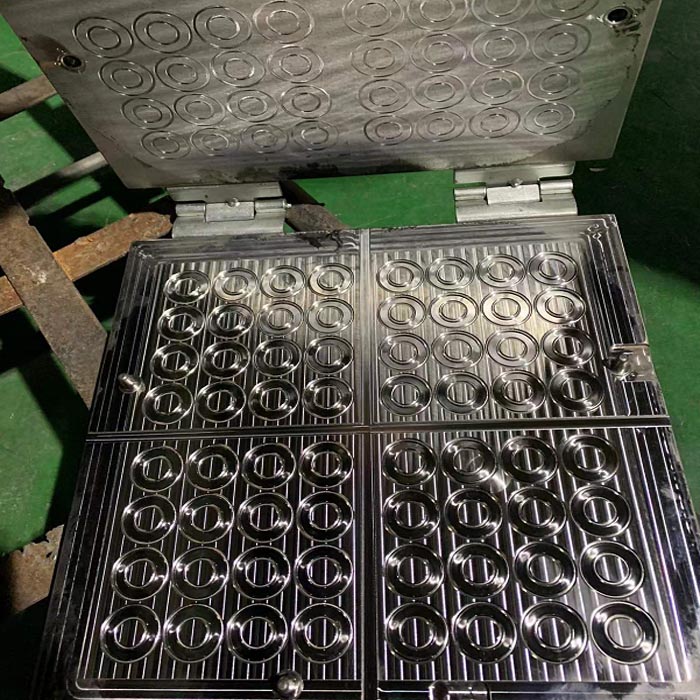
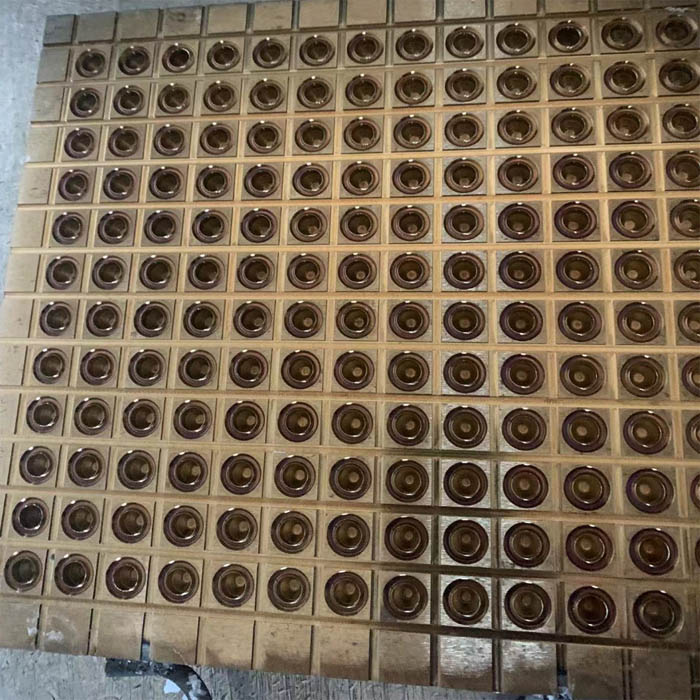
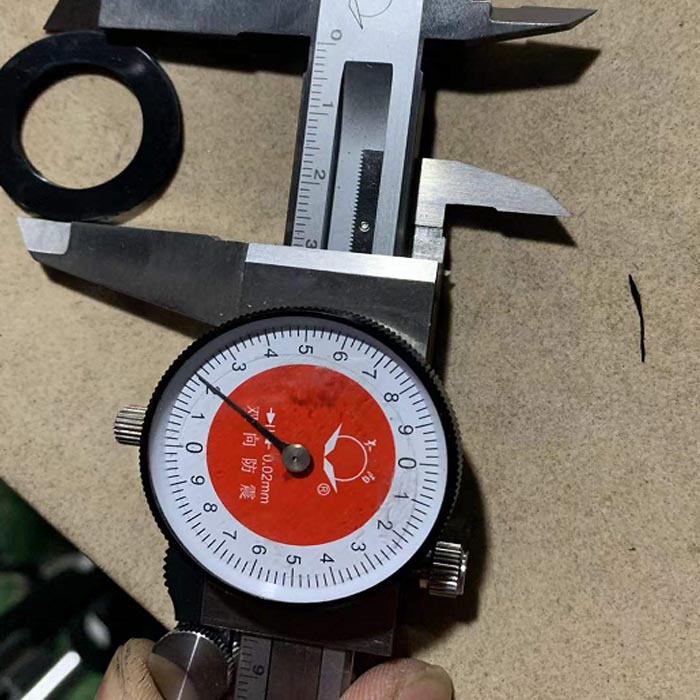
The product made from rubber as raw material and vulcanized under high temperature and high pressure with a mold is called a rubber model product. The larger one has automobile tires, and the smallest one has a lighter sealing ring with a diameter of only 50 millimeters. The mold material, dimensional accuracy, exhaust and mold opening difficulty, etc. all directly affect the quality, labor intensity, and production efficiency of rubber products. At the same time, the selection of mold material, heat treatment and other manufacturing processes, as well as the quality of mold assembly, directly affect the service life of the mold. Therefore, when designing the mold, firstly, we should carefully analyze and study the characteristics of the shape and structure of the rubber parts, and use this as a basis to select and design a reasonable mold structure, reasonable material and heat treatment process to meet the requirements of rubber products and the use of molds. It is required that the mold is easy to open after vulcanization, which can provide the production efficiency and the service life of the mold, thereby improving the economic benefit.
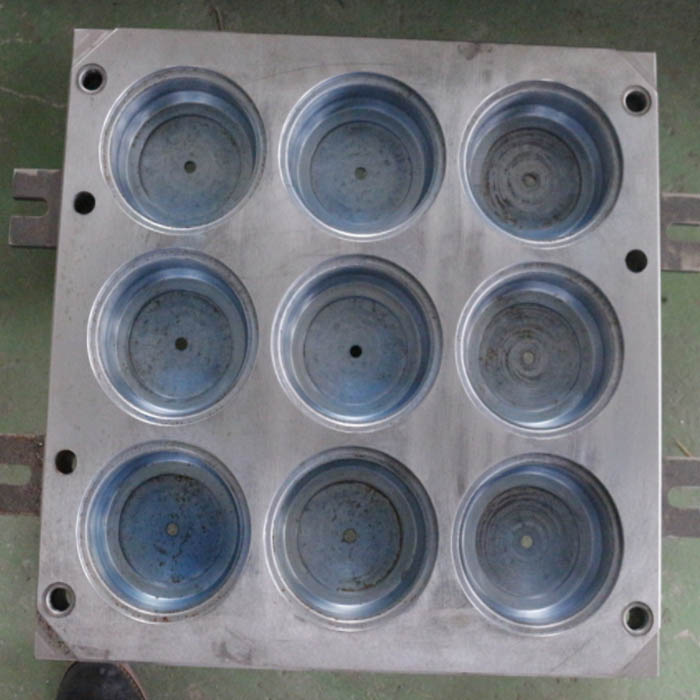
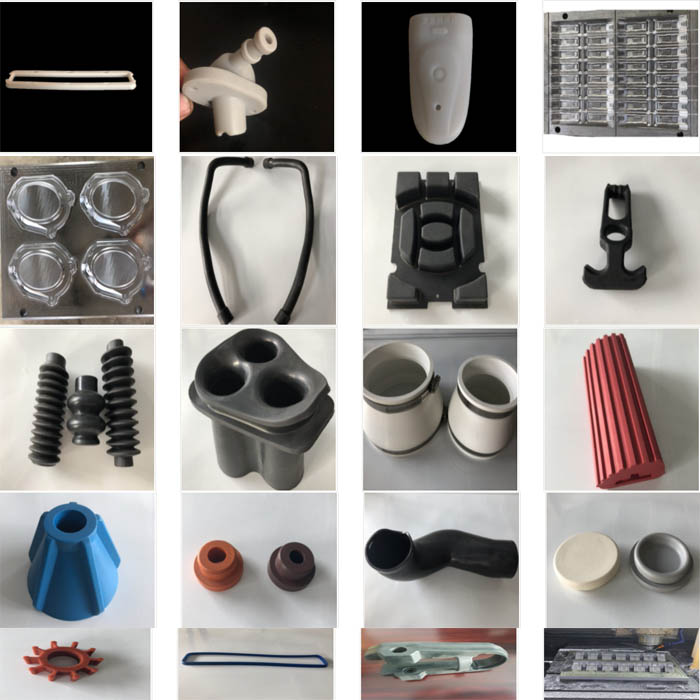
MB/Wechat/Whatsapp:+0086-13456489912
sophiemould@foxmail.com
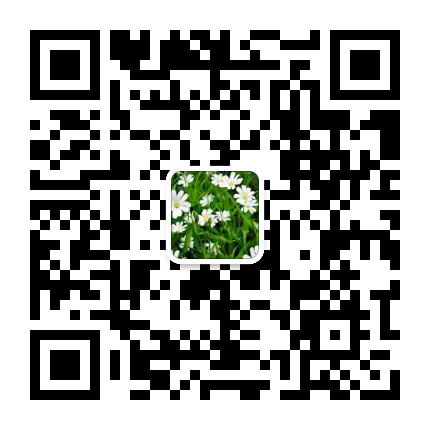
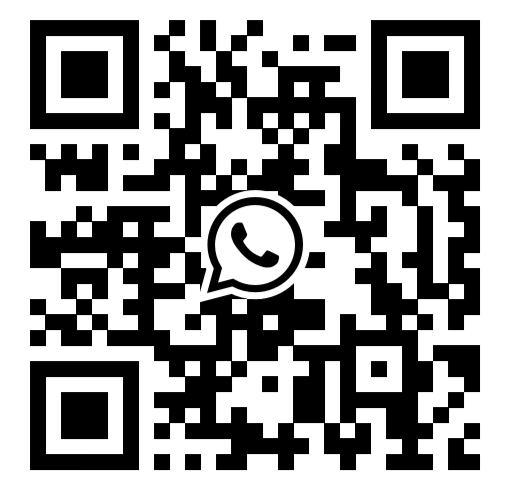
-
Mich Model Advanced Combat Ballistic Helmet mol...
-
Precision Plastic Injection Mould for Juicer Ma...
-
38MM Screw cap mould plastic injection closure ...
-
Anti-Theft Manhole Covers molding with Frame mould
-
taizhou Household commodity plastic injection a...
-
China taizhou female male Tee pipe fitting mold...